Introduction
Industrial coatings are high-performance finishes designed to protect structures and equipment from harsh environments, extend service life, and maintain functionality across a wide range of industrial applications. Let’s look at their types, application methods and failure mechanisms.
What are Industrial Coatings?
Industrial coatings are specialized paints or coatings designed for industrial applications, offering enhanced protection against harsh conditions, chemicals, and abrasion, and serving as a barrier against corrosion, rust, and deterioration. Along with providing a decorative finish, these coatings play a critical role in protecting structural integrity, extending service life, and maintaining the performance of components across a wide range of industries. Typically applied to metal, concrete, plastic, or composite surfaces, industrial coatings are indispensable in sectors such as oil and gas, marine, automotive, aerospace, infrastructure, manufacturing, and power generation.
The primary objectives of industrial coatings include:
- Corrosion protection: To prevent oxidation and electrochemical reactions.
- Chemical resistance: To provide barrier properties against aggressive substances.
- Abrasion and wear resistance: To protect high-contact surfaces.
- Thermal insulation or conductivity: For heat-sensitive or heat-dissipating components.
- UV and weather resistance: Especially critical in outdoor or harsh environments.
- Hygienic and cleanability: For food, pharmaceutical, and cleanroom applications.
Advanced coatings are also tailored for specialized functions such as non-stick behavior, electrical conductivity, or anti-microbial protection. Due to their multifunctional capabilities, the selection and application of industrial coatings require an in-depth understanding of materials science, surface chemistry, and environmental exposure conditions.
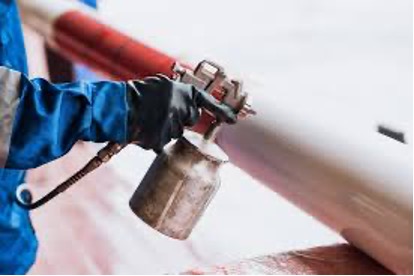
Types of Industrial Coatings

Industrial coatings can be broadly classified based on their chemical composition, binder type, and functional properties. The most common categories include metallic coatings, organic coatings, inorganic coatings, and hybrid systems. Let’s have a look at these industrial coatings and their mode of application in detail:
Metallic Coatings
Metallic coatings involve the deposition of a metal or alloy layer onto a substrate to provide corrosion resistance, sacrificial protection, or surface hardness. They are widely used in structural steel, pipelines, machinery, and high-wear components.
a. Galvanization (Zinc Coating)
Galvanization is the process of applying a zinc layer to steel via hot-dip or electroplating methods. Zinc acts as a sacrificial anode, corroding preferentially to protect the steel beneath. Hot-dip galvanizing, compliant with ASTM A123, provides thick, adherent coatings suitable for outdoor infrastructure.
b. Thermal Spray Coatings
Thermal spraying techniques such as High-Velocity Oxy-Fuel (HVOF) and Plasma Spray deposit molten or semi-molten metal particles (e.g., Zn, Al, NiCr) onto a surface to create dense, adherent coatings. These are used extensively in aerospace turbines, boiler tubes, and petrochemical plants.
c. Electroplating
Electroplating involves the electrodeposition of metals like chromium, nickel, or cadmium from an electrolyte solution onto a substrate. It offers excellent aesthetics and moderate corrosion resistance. However, cadmium’s toxicity has led to regulatory restrictions.
d. Cladding and Hardfacing
Cladding refers to bonding a corrosion-resistant metal layer (e.g., Inconel, stainless steel) onto a cheaper substrate via welding or roll bonding. Hardfacing involves depositing wear-resistant alloys such as Stellite or tungsten carbide by welding to enhance abrasion resistance.
Organic Coatings
Organic coatings are polymer-based films applied in liquid or powder form. These are the most versatile and widely used category, offering excellent barrier protection, adhesion, and aesthetic appeal.
a. Epoxy Coatings
Epoxies are thermosetting polymers formed by the reaction of epoxy resins with curing agents. Renowned for their excellent adhesion, chemical resistance, and mechanical properties, epoxies are the backbone of pipeline coatings, tank linings, and marine applications. Variants include fusion-bonded epoxy (FBE), solvent-free epoxies, and glass-flake epoxies.
b. Polyurethane Coatings
Polyurethanes offer outstanding UV resistance, gloss retention, and abrasion resistance. Their flexibility makes them suitable for bridges, offshore platforms, and topcoats over epoxy primers. Aliphatic polyurethanes are preferred for exterior use, while aromatic types are used in less demanding settings.
c. Acrylic Coatings
Acrylic polymers, either solvent-based or waterborne, provide fast-drying, color-stable finishes. Though less chemically resistant than epoxies or polyurethanes, they are used in architectural, automotive, and signage applications.
d. Polyester and Fluoropolymer Coatings
Polyester coatings, including powder coatings, are used for appliances and general industrial finishes. Fluoropolymers (e.g., PVDF, PTFE) offer extreme chemical and UV resistance, making them ideal for chemical plants, solar panels, and architectural cladding.
Inorganic Coatings
Inorganic coatings are typically ceramic or silicate-based systems that provide exceptional heat and corrosion resistance. They are often used in environments where organic systems would degrade.
a. Silicate-Based Coatings
Inorganic zinc-rich silicate coatings combine the sacrificial protection of zinc with a silicate binder that offers high temperature and solvent resistance. They are commonly applied as primers in three-coat systems for structural steel.
b. Ceramic Coatings
Ceramic coatings, such as alumina or zirconia, are deposited using plasma spray or chemical vapor deposition (CVD). These provide thermal barrier protection up to 1500°C and are essential in aerospace and power generation turbine components.
c. Glass Flake Coatings
Glass flake-reinforced coatings, though often considered hybrid, use inorganic glass flakes in epoxy or polyester matrices. They enhance impermeability and chemical resistance, particularly in flue gas desulfurization units and storage tanks.
Hybrid and Advanced Coatings
Hybrid coatings integrate properties from multiple classes to address complex service environments. They often combine organic and inorganic chemistries to leverage synergistic effects.
a. Epoxy-Polyurethane Systems
This widely used system employs an epoxy primer for adhesion and corrosion resistance, topped with a polyurethane for UV and abrasion protection. It offers comprehensive performance for offshore platforms, ship hulls, and bridges.
b. Sol-Gel Coatings
Sol-gel coatings use metal alkoxides that undergo hydrolysis and condensation to form a silica or titania network. These ultra-thin, transparent coatings provide anti-corrosion, anti-fouling, and self-cleaning functionalities for optics, electronics, and biomedical devices.
Surface Preparation and Pretreatment of Industrial Coatings
The efficacy and longevity of industrial coatings are directly influenced by the condition of the substrate prior to application. Surface preparation is a critical determinant of coating performance, influencing adhesion strength, corrosion resistance, and overall durability. Various pretreatment processes are employed based on the substrate material, environmental exposure, and intended service life of the coating system. They are given below:
Abrasive Blasting
Abrasive blasting, also known as grit blasting or sandblasting, is one of the most prevalent surface preparation methods for metallic industrial coatings. It involves the high-velocity projection of abrasive media—such as aluminum oxide, steel grit, garnet, or silica—against the surface to remove mill scale, rust, old coatings, and other contaminants. This process not only cleans the surface but also imparts a controlled roughness (anchor profile) that promotes mechanical interlocking of the coating.
The Sa standards developed by the Swedish Corrosion Institute (SIS), later adopted by ISO 8501-1, are widely used to specify cleanliness levels achieved by blasting. For example, Sa 2.5 (very thorough blast cleaning) is commonly specified for protective coatings in corrosive industrial environments.
Over-blasting can cause excessive roughness or embed abrasives into softer substrates, negatively affecting adhesion or causing underfilm corrosion.
Degreasing and Solvent Cleaning
Organic contaminants such as oil, grease, and machining fluids must be eliminated prior to coating, as they interfere with adhesion and may cause localized coating failure. Degreasing can be accomplished using:
- Solvent cleaning (SSPC-SP1): Involves application of organic solvents (e.g., acetone, toluene, MEK) or water-based surfactants followed by wiping or rinsing.
- Alkaline cleaning: Employs sodium hydroxide-based solutions to emulsify oils and saponify fatty contaminants.
- Steam cleaning and pressure washing: Useful for large-scale equipment or heavily soiled surfaces.
Solvent residues and cleaner by-products must be thoroughly rinsed to avoid adverse reactions with subsequent coatings.
Phosphating
Phosphating is a chemical pretreatment used predominantly on ferrous substrates to enhance corrosion resistance and promote coating adhesion. It involves the reaction of the metal surface with a phosphoric acid solution containing divalent metal ions (Zn²⁺, Mn²⁺, Fe²⁺), resulting in the formation of an insoluble crystalline phosphate layer.
There are various types of phosphate coatings:
- Zinc phosphate: Most widely used, offering excellent paint adhesion and moderate corrosion resistance.
- Manganese phosphate: Preferred for wear resistance in lubricated environments.
- Iron phosphate: Economical option with thinner coatings, suitable for low-corrosion indoor applications.
Phosphating also reduces friction during forming and improves paint wetting and coverage. Typically used before powder coating, e-coating, and certain liquid-applied coatings.
4. Conversion Coatings
Conversion coatings are chemical treatments that form a passive, corrosion-resistant layer through chemical transformation of the substrate surface. These include:
- Chromate conversion coatings: Used primarily on aluminum and zinc substrates. They form a thin, passive layer of chromium oxides and hydroxides that inhibit corrosion. However, due to the toxicity of hexavalent chromium (Cr⁶⁺), their use is now restricted under RoHS and REACH regulations, pushing industries toward trivalent chromium (Cr³⁺) or non-chromate alternatives.
- Anodizing (for aluminum): A controlled electrochemical oxidation that forms a dense oxide layer. Hard anodizing can significantly improve wear and corrosion resistance and serves as a base for dyeing or sealing.
- Silane-based treatments: Gaining prominence as environmentally benign adhesion promoters and corrosion inhibitors, silane coupling agents form covalent bonds with both the metal and the organic coating.
The choice of pretreatment depends on multiple factors, including the substrate type, expected environment (e.g., marine, chemical process, high-humidity), coating chemistry, and regulatory compliance.
Now let’s look at the failure mechanisms in industrial coatings.
Failure Mechanisms in Industrial Coatings
Despite meticulous design and execution, industrial coatings are susceptible to various failure modes. Understanding these mechanisms is vital for preventive maintenance, failure analysis, and specification improvements. The primary coating failure modes include blistering, delamination, corrosion under coating (CUC), and erosion.
1. Blistering
Blistering in industrial coatings is characterized by the localized detachment of the coating in the form of dome-shaped swellings due to the accumulation of vapor, gas, or liquid beneath the film. The phenomenon often arises due to:
- Osmotic pressure: When the coating contains hydrophilic contaminants or permeable defects, water ingress through diffusion may lead to osmotic blistering.
- Volatile entrapment: Improper curing or application over contaminated surfaces can trap solvents or moisture, which vaporize and expand under service temperatures.
- Electrochemical reactions: Especially under cathodic protection systems, hydrogen gas evolution at coating defects can contribute to blister formation.
Blistering is typically evaluated using ASTM D714, which categorizes blister size and frequency. Prevention requires stringent control of surface preparation, coating selection (low water vapor transmission rate), and proper curing practices.
2. Delamination (Disbonding)
Delamination refers to the cohesive or adhesive failure of the coating, resulting in separation from the substrate or between coating layers. Common causes include:
- Poor surface preparation: Inadequate surface cleaning or profile results in weak adhesion.
- Differential thermal expansion: Mismatch in thermal coefficients between substrate and coating induces internal stresses under cyclic thermal loads.
- Intercoat incompatibility: Application of chemically incompatible layers (e.g., solvent-borne over uncured waterborne) can weaken adhesion.
- Moisture ingress: Capillary penetration of water or aggressive ions (Cl⁻, SO₄²⁻) can attack the interface, especially in marine environments.
Delamination can be catastrophic in pipeline coatings, offshore structures, and aircraft components, where localized failure may lead to rapid underfilm corrosion.
3. Corrosion Under Coating (CUC)
Corrosion under coating is a pervasive failure mechanism that undermines the primary objective of protective coatings. It often remains undetected until widespread damage has occurred. CUC can be initiated at coating defects such as pinholes, scratches, or weak interfaces. The driving factors include:
- Electrolyte ingress: Water and ions penetrate through micro defects or at damaged edges.
- Cathodic delamination: Under impressed current cathodic protection (ICCP), hydrogen evolution at holidays can cause coating lift-off and metal loss.
- Microbial activity: In water tanks and marine environments, microbiologically influenced corrosion (MIC) can exacerbate CUC, especially under biofilms.
4. Erosion
Erosive wear results from the mechanical interaction of high-velocity particles or fluids with the coated surface, leading to material removal. This mechanism is especially relevant in:
- Hydrocyclones and pump impellers (mining and mineral processing)
- Turbine blades and ducting systems (power generation)
- Pipe bends and elbows (abrasive slurry transport)
Coatings in such environments must possess high hardness, resilience, and impact resistance. Thermal spray coatings, ceramic-reinforced epoxies, and polyurea elastomers are typical selections for erosion resistance.
Erosion is often compounded by corrosion-erosion synergy, where mechanical wear continuously removes protective oxide films, exposing fresh metal to corrosion, leading to an accelerated rate of material degradation.
5. Cracking
Cracking refers to the formation of fractures within the coating, which can propagate through its thickness and expose the underlying substrate. It may occur in several forms:
- Mud cracking: A network of fine cracks resembling dried mud, typically due to excessively thick application or rapid solvent evaporation during curing.
- Thermal cracking: Arises from cyclic thermal stresses when the coating and substrate have mismatched coefficients of thermal expansion.
- Mechanical cracking: Induced by substrate deformation, impact loading, or vibrational fatigue in dynamic structures.
- Shrinkage cracking: Occurs during curing of high-solids or thermosetting coatings, especially epoxies, where volumetric contraction exceeds tensile strength.
Cracks act as pathways for moisture and corrosive species, leading to rapid underfilm corrosion.
6. Undercutting
Undercutting refers to the lateral propagation of corrosion beneath a coating from a defect or holiday. Even a small breach can serve as a nucleus for undercutting, especially in marine or high-salinity environments.
It is often aggravated by:
- Poor edge protection (thin or discontinuous coating at sharp corners)
- Inadequate surface preparation near fasteners or welds
- Weak adhesion and lack of barrier properties
High-performance barrier systems and edge-sealing techniques are critical for undercutting resistance.
Industrial Coatings Selection Criteria
Selecting the appropriate industrial coating system is a critical engineering decision that directly impacts component durability, asset longevity, operational safety, and total life-cycle cost. The selection process must consider the interplay between the service environment, substrate material, thermal and mechanical stresses, chemical exposure, and maintenance accessibility. A misalignment between coating specification and operating conditions often leads to premature failure, necessitating costly rework and asset downtime.
1. Service Environment
The operational environment exerts a dominant influence on coating performance. Environments are generally categorized based on the ISO 12944-2 classification, which delineates atmospheric corrosivity into categories C1 to C5 and CX (for extreme conditions), along with immersed and chemical environments. Selecting coatings that align with these categories ensures optimal corrosion protection.
Examples:
- C3 (Urban/Mild Industrial): Epoxy primer with polyurethane topcoat may suffice.
- C5-I (High Industrial): High-build epoxy with zinc-rich primer and fluoropolymer or polysiloxane topcoat.
- CX (Marine Splash/Offshore): Thermal Sprayed Aluminum (TSA) with sealers and high-performance barrier topcoats.
Other environmental factors to consider include:
- Humidity and condensation cycles
- UV exposure
- Abrasive particles in air (windblown sand, soot)
- Microbial or fungal growth potential
In submerged environments, such as wastewater treatment, marine hulls, or chemical storage tanks, coatings must resist prolonged immersion, hydrolysis, microbial degradation, and biofouling.
2. Substrate Material
The nature of the substrate—whether metallic, polymeric, composite, or concrete—greatly influences coating adhesion and compatibility. Substrate characteristics affect surface pretreatment requirements, chemical bonding mechanisms, and electrochemical behavior.
Metal Substrates:
- Carbon steel: Prone to corrosion; often requires zinc-rich primers or metalized coatings for cathodic protection.
- Stainless steel: Passive but may require abrasion or chemical pretreatment to improve adhesion.
- Aluminum and zinc: Susceptible to filiform corrosion; benefit from chromate conversion or compatible primers.
Non-metallic Substrates:
- Concrete: Porous and alkaline; requires penetration sealers or surface leveling before coating.
- Plastics and composites: Low surface energy materials often demand flame or plasma treatment, or the use of specialized adhesion promoters.
Some coatings may cause galvanic corrosion when used on dissimilar metal assemblies; for instance, certain copper-based antifouling paints may accelerate corrosion in aluminium structures if improperly isolated.
3. Temperature and Thermal Cycling
Coating systems must be capable of withstanding both the absolute temperature and the rate/frequency of thermal cycling. Key considerations include:
Service Temperature Limits:
Each coating has a maximum service temperature beyond which its chemical integrity degrades. For example:
- Acrylics: ~90–120°C
- Epoxies: ~120–150°C (some novolac epoxies up to 230°C)
- Silicone-based coatings: >250°C, suitable for exhaust systems and furnaces
- Ceramic or metal-based thermal barrier coatings (TBCs): >1000°C in gas turbines
Thermal Shock and Cycling:
Repeated heating and cooling cycles can cause:
- Expansion mismatch between substrate and coating → leading to cracking or delamination.
- Accelerated oxidation at coating defects → especially in high-temperature corrosion environments (e.g., sulfidation, carburization).
In these scenarios, coatings with low thermal expansion, good elasticity, and phase stability—such as metallic aluminides or yttria-stabilized zirconia—are preferred.
4. Chemical Exposure and Aggressiveness
Exposure to chemicals such as acids, alkalis, solvents, oxidizers, or process gases severely limits coating selection. Compatibility must be evaluated for:
- Concentration
- Temperature of exposure
- Duration (intermittent vs. continuous)
- Contact mode (immersion, splash, vapor)
Example Scenarios:
- Sulfuric acid exposure (pH < 1): Requires vinyl ester, fluoropolymer, or novolac epoxy systems.
- Alkaline CIP cleaners in food plants: Alkali-resistant polyurethane or polyaspartic coatings.
- Solvent tanks (e.g., toluene, ketones): Require solvent-resistant phenolic epoxies or PFA linings.
- Chlorinated environments (e.g., bleach plants): Coatings must be resistant to oxidative degradation.
Chemical resistance guides from coating manufacturers or databases such as NACE MR0103 help guide material selection for aggressive process environments.
5. Mechanical and Abrasive Loads
Coatings must resist:
- Abrasion and impact: High solids epoxies, ceramic-reinforced linings, and thermally sprayed carbides are suitable for slurry lines and mining equipment.
- Flexural stress or vibration: Elastomeric coatings like polyurethanes and polyureas are more tolerant of dynamic movement.
- Cavitation erosion (e.g., pump impellers): May require elastomeric coatings or metal-matrix composites.
Shore hardness, tensile elongation, and abrasion resistance (measured via ASTM D4060 Taber test or ASTM G65 for dry sand abrasion) are critical mechanical selection criteria.
6. Application Method and Site Conditions
Coating performance is tied to the application process, which is influenced by site accessibility, atmospheric conditions, and available equipment. Examples include:
- Shop-applied coatings: Allow better environmental control (e.g., powder coating, e-coat).
- Field-applied systems: Require tolerance to ambient humidity and temperature variability.
- Fast-curing systems (e.g., polyurea): Useful for shutdowns or overnight applications.
Surface-tolerant coatings (e.g., surface-tolerant epoxies) are often used where blasting is restricted or surface cleanliness is sub-optimal, such as in refurbishment of in-service pipelines.
7. Regulatory and Environmental Compliance
Coatings must comply with:
- VOC regulations (EPA, EU Decopaint Directive)
- REACH/RoHS (restrictions on Cr⁶⁺, Pb, Cd in coatings)
- FDA/USDA approval for food contact surfaces
- NSF 61 certification for potable water contact
8. Cost and Life-Cycle Economics
While initial cost is a consideration, emphasis should be placed on total life-cycle cost (LCC), which accounts for:
- Initial material and application costs
- Frequency and cost of maintenance or recoating
- Risk and cost of failure (downtime, contamination, safety incidents)
- Disposal and environmental costs
For critical infrastructure—pipelines, offshore structures, chemical plants—specifying high-performance, longer-lasting systems is usually more economical over the asset’s lifespan.
Conclusion
Industrial coatings are far more than mere finishes—they are engineered protection systems vital to ensuring structural integrity, chemical resistance, and long-term durability in demanding service environments. Their successful application requires a deep understanding of material compatibility, environmental conditions, mechanical stresses, and regulatory frameworks. By selecting the appropriate coating system based on comprehensive performance criteria rather than cost alone, engineers can significantly enhance asset reliability, safety, and total life-cycle value across industries ranging from oil and gas to food processing and power generation.