Types of report preparation and reviewing
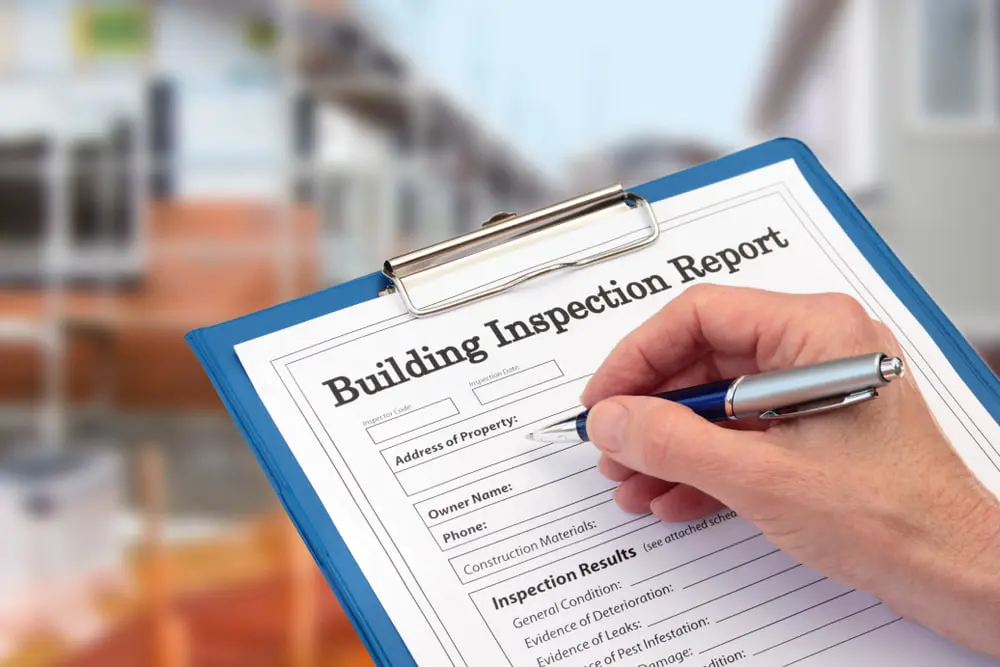
As a dynamic player in every project, your role as a Coating Inspector is truly obligatory. Each day, you have the captivating prospect to create and review a wide array of documents that are crucial for project success. Regardless of your specific role within the project, your proficiency ensures that all documentation aligns with the utmost standards.
From start to finish, you’ll be crafting documents independently and accurately reviewing others to ensure they meet the project’s stringent requirements. Your work isn’t just for project acceptance; it’s about guaranteeing that all coatings adhere to industry standards flawlessly.
These documents you’re mastering include inspection reports, compliance records, quality assurance files, and more—each one ensuring top-notch results.
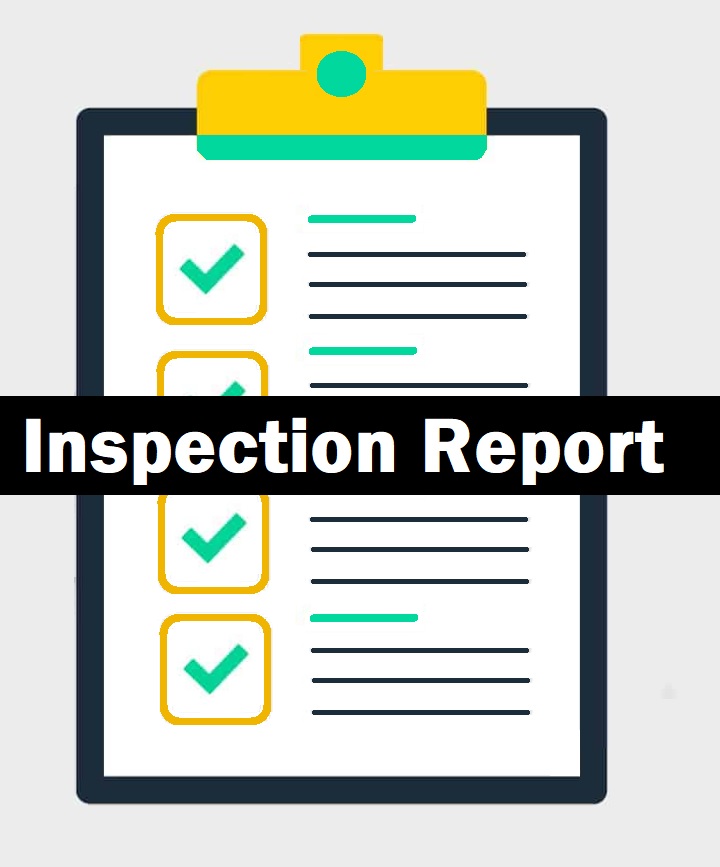
What documents / Forms Inspector shall make?
- Daily Log
- Daily Inspection Report
- Daily Weather monitoring report
- Weekly Inspection Summary Report
- Monthly Inspection Summary Report
- Non-Conformance Report (NCR)
- Corrective Action Report (CAR)
- Surveillance Report
- Adhesion Test Report (Either Coating Representative or QC Inspector)
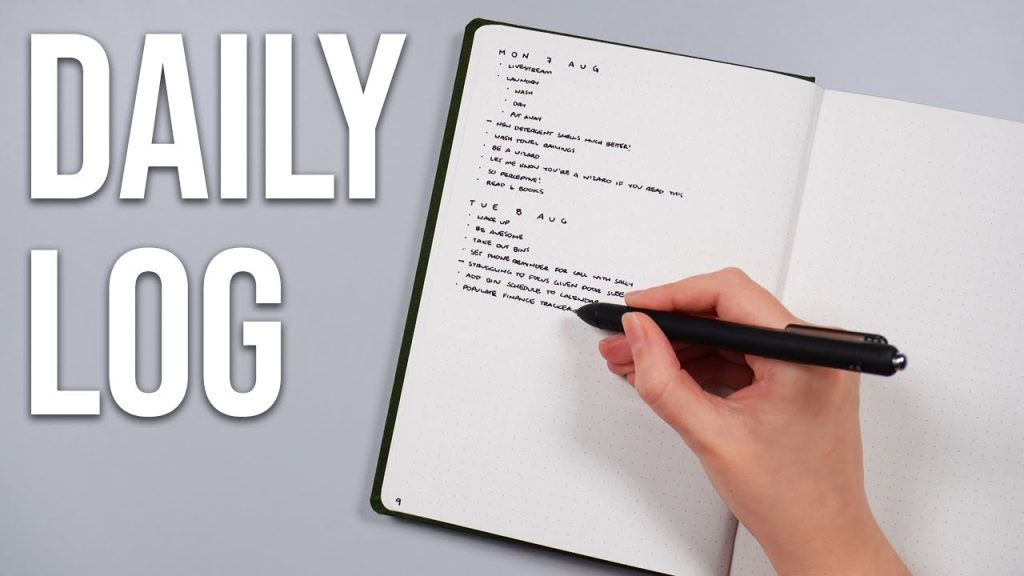
Difference between Daily Log and Daily Inspection Report
We herewith showcase some light on a topic that has sparked quite an exciting debate among coating inspectors on the distinction between a Daily Logbook and a Daily Inspection Report. It’s clear there’s been some confusion surrounding these tools, but no worries, we’re here with all the details to clear things up.
The main differences boil down to their purpose and structure. The Daily Logbook serves as your ongoing DIARY a comprehensive record of all activities, observations, Testing Values (Qualitative or Quantitative) and interactions during your inspection. On the other hand, the Daily Inspection Report is more of a snapshot which is a FORMAL & APPROVED document summarizing specific findings and recommendations from each day’s work in which all the information is copied and pasted from Logbook.
Both tools are invaluable in ensuring quality control and maintaining thorough documentation, so understanding how they complement each other will only enhance our effectiveness in the field.
Daily Log or Logbook
Logbook is a temporary usage of information in which all the information shall be transferred into Daily Inspection report on the same day or immediately. Because Daily Inspection report is impractical to carry at the site, which may damage on the whole day, thus Logbook is being used as temporary record purposes.
Inspector shall record his entire observations, findings, anomalies, weather condition, pre-treatment outcome, Surface preparation result, Surface Profile values, Salt values, Dust rating etc., during the process of stage-by-stage assessment on the daily log.
Daily Inspection Report
Daily Inspection Report (DIR), which plays a crucial role in our Inspection workflow. Remember, DIR is the official report and requires prior approval from the client or owner before it can be utilized. It’s essential that we only work with the updated revision of this report throughout the entire project duration.
The process is straightforward: after completing routine inspection activities, each Inspector will prepare a DIR based on the recorded information from their daily logs. This ensures that all data is accurate and up-to-date.
To ensure compliance with project standards, each DIR will then be verified by Client QA Inspector for approval. Their acceptance confirms that we are on track and aligned with project requirements.
Daily Weather monitoring report
In general, many inspectors recording daily weather condition information on the daily log or DIR directly. However, few project demanding this information (4 or 6 times) shall be recorded in separate form that shall be attached to the Daily Inspection report.
Weekly Inspection Summary Report
On a weekly basis, the Inspector shall record all the complete inspection activities in this form that shall be submitted to the QC Manager which is being practiced as a part of Quality Assurance Management system. In this manner, any left out or partial inspection and any non-conformance shall be easily identified and followed up.
Non-Conformance Report (NCR)
As a protocol, the appointed Inspector has the authority to issue a Non-Conformance Report (NCR) when activities are found deviating from project requirements. Such a situation typically arises when issues remain unrectified or if there is non-compliance with specified standards. It is critical to understand that this NCR process is not only costly but also cumbersome for all parties involved.
To avoid these complications, it is imperative that any deviations are addressed promptly and rectified up to the satisfaction of our inspection team, as outlined in the project specifications. This proactive approach will help us maintain high standards and avoid unnecessary delays or expenses.
To alleviate unnecessary and costly remedial actions, the concerned team reviews all project requirements thoroughly and takes immediate corrective actions where necessary. Our goal is to work collaboratively towards successful project completion without resorting to NCRs.
Monthly Inspection Summary Report
Same as weekly report, this monthly report perhaps prepared by Inspector and submitted to the Quality control department Head. This report would be useful in the client / contractor progress meeting.
Surveillance Report
Still this report is being confused by many inspectors with coating survey, coating surveillance report. Those reports are prepared in maintenance coating and part and parcel of survey and coating failure analysis.
The surveillance reports are designed to empower inspectors to observe and monitor ongoing activities without the need for an official inspection. During this process, any findings and potential improvements are meticulously documented in a surveillance report, which is then issued to you for immediate resolution.
By addressing these reports promptly and taking proactive measures, contractors can effectively avoid costly Non-Conformance Reports (NCR) in the future. This not only ensures compliance with project standards but also significantly reduces the risk of delays and additional expenses.
Emphasising CARs as a tool for continuous improvement will result in more efficient project execution and ultimately, greater success for all parties involved.
Corrective Action Report (CAR)
A CAR is an essential document designed to record and track any issues or nonconformities that arise. It serves not only as a record but also as a structured approach to resolving these problems effectively. In coating industry, utilizing a CAR can significantly enhance the coating process by identifying and rectifying issues promptly.
The primary purpose of implementing a CAR includes:
- Root cause identification.
- Corrective action implementation
- Prevention measures and action
By adopting this systematic approach, we not only resolve current challenges but also fortify our processes against potential future disruptions, ensuring consistent quality and efficiency.
The integration of CARs into our workflow will drive significant improvements and uphold our commitment to excellence.
Adhesion Test Report (Either Coating Representative or QC Inspector)
The present procedure for conducting and reporting the Adhesion Test is time-consuming and cannot be effectively integrated into our Daily Inspection Report (DIR). While inspectors can include the acceptance criteria in the DIR, detailing the entire process along with photographic evidence is not feasible due to time constraints.
To ensure thorough documentation and maintain our quality standards, it is worthwhile to implement a separate reporting system specifically for the Adhesion Test. This report could be prepared by either a dedicated QC inspector or directly by the coating manufacturer. This approach would streamline our inspection process and ensure that all necessary details are meticulously recorded without burdening our daily operations.
Implementing this change will provide us with comprehensive records of each test, enhancing traceability and accountability while allowing inspectors to focus on their core responsibilities.
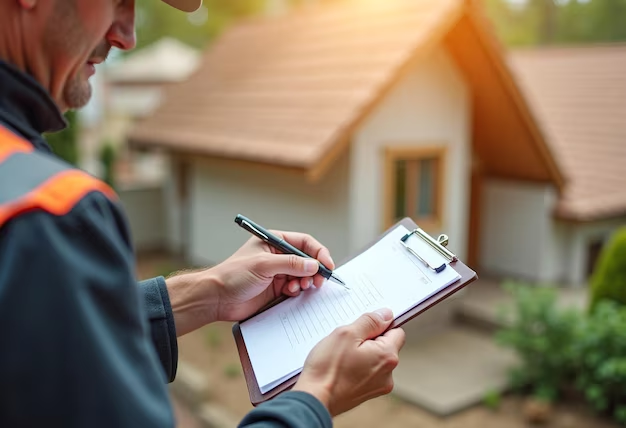
What documents / Forms Inspector shall review?
- Project Documents (i.e. Specification / PDS / MSDS / ITP / Procedures / MAR)
- Coating & Abrasive Batch Certificates
- Third party Laboratory reports
- Manufacturer specific recommendations
- Equipment / Instrument Calibration certificates
- Inspection Instruments manual / Instructions
- Third party experts / Consultant Report
Project Documents
Before embarking on any coating projects, it is crucial that all inspectors thoroughly prepare by obtaining, reading, understanding, and interpreting all project-approved documents. This includes the specification, Product Data Sheet, Safety Data Sheet, Inspection and Test Plan, Procedures (method statement), Material Approval Request, among others.
By ensuring comprehensive familiarity with these documents, inspectors can effectively oversee project execution and uphold the highest standards of quality and safety. This preparation is key to preventing misunderstandings or errors that could impact project success.
Coating & Abrasive Batch Certificates
Before proceeding with any production activities, it is essential that the Inspector thoroughly reviews all coating and abrasive-related batch certificates, test certificates, or chemical analysis reports. This review is crucial to ensure that all materials comply with the specific requirements and standards of our project.
Adhering to this protocol will not only guarantee the quality and safety of our work but also prevent any potential setbacks or non-compliance issues down the line. Inspector adherence in this matter is vital for the success of our project.
Third party Laboratory reports
As we move forward with our project, it is crucial to ensure that all aspects of the coating processes are thoroughly evaluated and executed to the highest standards. Coating Inspector shall review all third-party laboratory reports on every coating projects. This includes assessments on abrasive analysis, coating generic analysis, and coating failure analysis.
By implementing these reviews throughout the project, we can ensure consistent quality and address any potential issues proactively well in advance. This strategic oversight will not only enhance the durability and performance of our coatings but also contribute significantly to the overall success of our project.
Manufacturer specific recommendations
On few occasions, especially for specific or critical coating system, the manufacture shall provide application instructions or recommendation, that shall be reviewed and implemented by coating inspector.
In our ongoing efforts to ensure the highest quality and performance of our coating systems, Inspector should emphasize the importance of adhering to application instructions or recommendations provided by the manufacturer. This is particularly crucial for specific or critical coating systems.
On several occasions, these tailored guidelines are essential for achieving optimal results and longevity of the coatings. Therefore, it is imperative that these instructions are carefully reviewed and implemented by our qualified coating inspectors. By doing so, we can guarantee that each application meets industry standards and fulfils its intended purpose effectively.
Equipment / Instrument Calibration certificates
Every inspector should emphasize the importance of proper calibration and documentation for our equipment and coating inspection instruments.
To ensure accuracy and compliance, it is crucial that all calibration certificates, whether issued by the manufacturer or third-party agencies, are thoroughly reviewed and archived by our Coating Inspector. This practice not only maintains the integrity of our processes but also aligns with industry standards.
Furthermore, please ensure that all calibrations are conducted in accordance with the instrument manufacturer’s recommendations or as specified in the project specifications. Adhering to these guidelines will significantly enhance our operational efficiency and reliability.
Inspection Instruments manual / Instructions
When these instruments arrive, it is imperative that we adhere strictly to the manufacturer’s specific instructions for handling and use. These guidelines are not merely suggestions, they are critical to ensuring the optimal performance and longevity of the equipment.
To this end, coating inspector will review all manufacturer instructions thoroughly. This step is essential as it ensures that every aspect of the handling procedures is understood and implemented correctly while the instruments are in service. By following these steps, we can assure quality outcomes and prevent any potential issues from arising due to mishandling or misuse.
Third party experts / Consultant Report
Amidst project execution, there may be an occasions where disagreements arise between the Contractor QC and Client QA regarding the alignment of actual work with specification requirements. While such debates are a natural part of ensuring high standards, it’s crucial to address them effectively to maintain the project’s quality.
To facilitate a resolution when these disagreements persist, Both parties may propose engaging a third-party expert or consultant. Their role will be to provide an unbiased analysis, including a detailed root cause investigation and recommended remedial actions. This expert report will serve as an objective basis for both parties to reach a common understanding and agreement. Everyone believe that by unanimously accepting the conclusions of this report, The project can ensure that the quality objectives are not only met but exceeded.
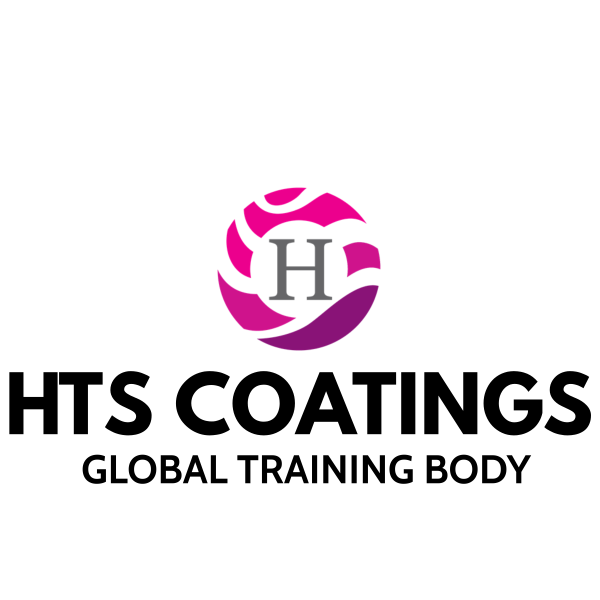