Introduction
Ever wondered why some coatings last for years while others peel, crack, or blister within months? The key lies in adhesion—the ability of a coating to bond effectively with the substrate. But adhesion isn’t the only factor at play; cohesion, or the internal strength of the coating itself, also plays a crucial role. Let’s explore how coatings adhere, the science behind it, and what causes adhesion failures.
The overall bond strength between the coating and the substrate is determined by two key material properties:
- Adhesion – The ability of the coating to adhere firmly to the surface of the substrate.
- Cohesion – The internal strength of the adhesive, ensuring the bond between its particles remains intact.
First, let’s look into adhesion of coatings in detail.
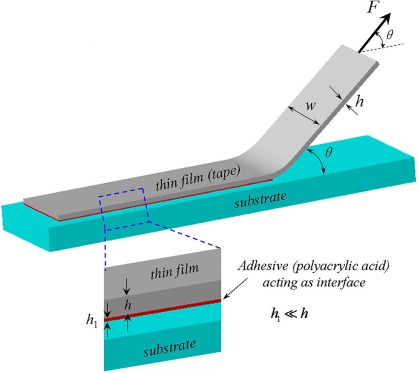
Adhesion of coatings refers to the ability of a coating (such as paint, varnish, or protective film) to firmly attach to the underlying substrate. It is a crucial property that determines the durability, performance, and longevity of the coating in various applications, including automotive, aerospace, construction, and industrial equipment.
Next, let’s try to understand how adhesion happens in various coatings and its underlying mechanisms.
Mechanisms of Adhesion in Coatings
Coatings adhere to substrates through a combination of different adhesion mechanisms, such as:
1. Mechanical Interlocking
The mechanical theory of adhesion explains that adhesion occurs when a material, such as a coating, penetrates and interlocks with the surface irregularities of a substrate. This physical anchoring enhances the bond strength between the coating and the substrate.
The adhesive (such as paint, glue, or coating) flows into microscopic pores, cracks, and rough textures on the substrate. Once cured or solidified, the adhesive becomes mechanically locked into these surface irregularities. The stronger the interlocking, the better the adhesion.
Surface roughness enhances adhesion by expanding the total contact area between the paint and the substrate. According to the mechanical adhesion theory, roughening a surface improves adhesion by creating a textured profile that allows for stronger mechanical interlocking i.e., roughening process provides “teeth” to the substrate, helping the coating anchor more effectively. Additionally, the increased surface area allows adhesion forces to develop over a larger region. However, roughening is only beneficial if the coating adequately wets the surface,
Factors Affecting Mechanical Adhesion
- Surface Roughness – A rougher surface provides more cavities for interlocking, improving adhesion.
- Surface Preparation – Techniques like sanding, grit blasting, or etching increase adhesion by creating more surface irregularities.
- Viscosity of the Adhesive – Low-viscosity coatings can penetrate surface pores more effectively, enhancing mechanical interlocking.
- Removal of Air and Contaminants – Trapped air, dust, or oils can prevent proper penetration and reduce adhesion strength.
2. Adsorption Theory
According to this theory, adhesion occurs due to attractive forces between the molecules of the coating and the substrate at their interface. These intermolecular forces, known as secondary or van der Waals forces, enable bonding when the paint molecules come into close molecular contact with the surface.
In addition to van der Waals forces, acid-base interactions and hydrogen bonding can further enhance adhesion. For effective adsorption, the paint film must maintain continuous contact with the substrate, allowing either van der Waals forces, acid-base interactions, or both to contribute to adhesion.
This level of molecular contact is achieved through a process called wetting. Complete and spontaneous wetting occurs when:
- The contact angle is 0°, indicating perfect surface coverage.
- The coating spreads uniformly across the substrate, forming a thin and even layer.
3. Diffusion Theory
This theory proposes that adhesion occurs when the adhesive and substrate are mutually soluble or when polymer chains from both materials interdiffuse at the interface. It is effective only when both materials have compatible molecular structures.
Example: Adhesion in thermoplastic polymers.
4. Chemical Bonding Theory (Covalent or Ionic Bonding)
The chemical bonding theory suggests that strong adhesion occurs when chemical bonds (covalent, ionic, or hydrogen bonds) form at the interface. Chemical interactions provide high bond strength and durability.
Example: Silane coupling agents in composite materials.
Adhesion Failure in Coatings: Causes and Mechanisms
Adhesion failure in coatings occurs when the bond between the coating and the substrate weakens or breaks, leading to delamination, peeling, or flaking. This failure compromises the coating’s protective and functional properties, reducing its overall performance and durability. Adhesion failure can result from several factors, including mechanical stresses, environmental influences, poor surface preparation, and chemical incompatibility. Here are the main causes of adhesion failure:
Poor Surface Preparation
One of the primary causes of adhesion failure is poor surface preparation. The presence of contaminants such as oil, grease, or dust on the substrate prevents proper bonding between the coating and the surface. Additionally, oxidation or corrosion on metal substrates can reduce adhesion, leading to premature failure. Surface roughness also plays a critical role in adhesion, since inadequately roughened surface prevents the coating from achieving proper mechanical interlocking as we discussed above. Without sufficient adhesion forces, the coating may fail even under normal operating conditions.
Want to know the best surface preparation methods? Check out our detailed article on surface preparation of coatings – SURFACE PREPARATION METHODS IN COATING INDUSTRIES
Lack of Proper Wetting
Another significant factor contributing to adhesion failure is inadequate wetting. If the coating does not spread uniformly over the substrate, it cannot establish molecular contact, which is essential for strong adhesion. A high contact angle, typically greater than 90 degrees, indicates poor wetting, resulting in weak bonding. In such cases, the coating may not adhere properly and can peel off under mechanical or environmental stress. Ensuring proper surface energy compatibility between the coating and substrate is crucial to achieving optimal wetting and adhesion.
Lack of Compatibility between Coating and Substrate
The compatibility between the coating and the substrate is another key consideration. A mismatch in chemical properties between the two materials can prevent proper bonding. For example, nonpolar coatings may struggle to adhere to polar substrates without appropriate surface treatment or the use of a primer. Inadequate primer selection can further weaken adhesion, making the coating more susceptible to peeling and failure over time. Ensuring that the coating system is chemically compatible with the substrate can significantly improve adhesion strength and long-term performance.
Improper Curing
Improper curing or drying of the coating can also lead to adhesion failure. If the solvent within the coating does not evaporate completely, volatile compounds may remain trapped, weakening the adhesion forces at the interface. Over-curing or under-curing can similarly affect the film’s integrity, reducing its ability to adhere effectively to the substrate. Proper control of curing conditions, including temperature and humidity, is essential to ensuring a fully bonded and durable coating.
Environmental Factors
Environmental factors such as moisture exposure, temperature fluctuations, and UV radiation can further contribute to adhesion failure. Moisture infiltration can lead to hydrolysis or swelling, causing the coating to lose adhesion over time. Temperature changes result in thermal expansion and contraction, creating stresses at the interface that weaken the bond. Additionally, prolonged exposure to UV radiation can degrade the chemical structure of the coating, making it more prone to failure. Protective measures, such as moisture barriers and UV stabilizers, can help mitigate these environmental effects.
Mechanical Stress
Mechanical stresses, including impact, abrasion, and differential thermal expansion, can accelerate adhesion failure. High levels of mechanical wear weaken the coating’s bond with the substrate, making it more likely to detach. Differential expansion between the substrate and the coating due to temperature variations can create significant stresses at the interface, ultimately leading to cracking and delamination. Choosing coatings with high flexibility and impact resistance can help mitigate these issues and enhance adhesion durability.
To prevent adhesion failure, several measures should be taken. Proper surface preparation, including cleaning, degreasing, and roughening, ensures that the coating achieves optimal bonding with the substrate. The selection of appropriate coatings and primers that are chemically compatible with the substrate is also essential. Additionally, curing conditions must be carefully controlled to allow the coating to fully develop its adhesive properties. Improving wetting characteristics through low surface tension coatings or surface treatments can further enhance adhesion strength. Finally, protecting the coating from environmental and mechanical stresses by applying corrosion inhibitors, UV stabilizers, and wear-resistant topcoats can significantly extend the coating’s lifespan and maintain its adhesion properties over time.
Additives to Improve Coating Adhesion
The adhesion of coatings is significantly influenced by several key factors that contribute to bond strength and durability. The primary factors that enhance adhesion include surface wetting, surface treatment, and the structural compatibility of the materials being bonded. Optimizing these parameters ensures strong interfacial interactions, thereby improving the coating’s performance under mechanical and environmental stress conditions.
In addition to these fundamental factors, various additives are incorporated into coating formulations to modify physical and mechanical properties, further enhancing adhesion. The role of these additives and their functional contributions are given below:
Adhesion Promoters: These compounds enhance bonding by exhibiting high affinity for both the substrate and the coating material. Their role is to establish a permanent and strong adhesive interface, thereby improving long-term adhesion performance.
Plasticizers: By softening the binder components in inks and coatings, plasticizers improve flexibility. This increased flexibility enhances the coating’s resistance to mechanical stress and impact forces during application and curing, minimizing the risk of adhesion failure.
Solvents: As volatile components, solvents help in reducing the viscosity of the binder, facilitating uniform application. By controlling the drying rate, solvents prevent defects such as blister formation, which can lead to adhesion failure.
Pigments and Extenders: These additives contribute to the physical properties of the coating, such as film hardness and water resistance, which indirectly enhance adhesion by improving the coating’s overall durability.
Wetting Agents: Comprising surfactants such as polysiloxanes, fluoro-based surfactants, and specialized wetting agents, these compounds address variations in surface tension. By improving substrate wetting, they enhance adhesion and promote uniform coating application.
Adhesion Test of Coating
When conducting any adhesion test, it is essential to determine the nature of bond failure. This can occur as either adhesive failure, where the coating detaches from the substrate at the interface, or cohesive failure, where the failure occurs within the coating film or the substrate itself.
Various testing methods are available to assess the strength of a coating’s bond to the substrate. Evaluating adhesion quality ensures that the coating maintains its performance and durability. The following section outlines the primary techniques used to test paint adhesion.
Cross-Cut Test
The ASTM D3359 standard outlines test methods for evaluating the adhesion of coating films to metallic substrates using a tape test. This assessment involves making precise cuts in the coating film, followed by the application and removal of pressure-sensitive tape to determine the degree of adhesion.
This method provides a straightforward approach to assessing how well a coating adheres to a substrate under mechanical stress. The cross-cut test is widely used in quality control and laboratory evaluations to ensure coatings meet required adhesion performance standards.
Scrape Test
The ASTM D2197 standard provides a method for evaluating the adhesion of organic coatings, such as paints, varnishes, and lacquers, when applied to smooth, flat surfaces. In this test, the coating is uniformly applied to a planar substrate and allowed to dry completely.
To assess adhesion strength, a rounded stylus or loop is gradually loaded with increasing force as it moves across the coated surface. The test continues until the applied force causes the coating to detach from the substrate. This method is particularly useful for determining the mechanical resistance of coatings under controlled conditions.
Pull-Off Test Using Portable Adhesion Testers
The ASTM D4541 standard outlines a method for measuring the pull-off strength of coatings using portable adhesion testers. Pull-off strength, also referred to as adhesion, is evaluated on rigid substrates such as metal, concrete, and wood.
This test assesses the bond strength of single or multiple coating layers applied to a smooth surface by subjecting them to tensile stress, rather than shear stress as measured in previous adhesion tests. A dolly is affixed to the coated surface, and an increasing load is applied until the dolly, along with the adhesive layers, detaches.
COHESION
Cohesion
Cohesion is the force of attraction between molecules of the same substance, which causes them to stick together. This intermolecular force plays a crucial role in various physical phenomena, such as surface tension. One of the most well-known examples of cohesion is the bonding between water molecules through hydrogen bonds. This interaction creates a thin, elastic layer on the water’s surface, allowing small insects to walk across without sinking.
One of the key characteristics of cohesion is surface tension, which results from the strong intermolecular forces within a liquid. This effect enables objects denser than water, such as a paperclip, to remain afloat when carefully placed on the surface. Another notable consequence of cohesion is the formation of spherical liquid droplets. Molecules within a droplet experience uniform attraction, causing the liquid to assume a shape that minimizes surface area. This property is particularly visible in raindrops and other liquid formations.
To prevent issues related to cohesive failure in materials, it is essential to monitor key parameters that influence cohesion. Cohesive failure occurs when a material fractures in such a way that a layer of adhesive remains on both surfaces, rather than detaching entirely from one of them. This type of failure can significantly impact the durability and performance of coatings and adhesives in structural applications.
Understanding Cohesive Failure and Its Impact
When the intermolecular forces within a substance weaken or break, the attraction between molecules diminishes, making the material more susceptible to separation under external stress. Cohesive failure occurs when the substrate itself breaks apart before the adhesive layer detaches, indicating that the internal strength of the material is compromised. A high rate of cohesive failure often leads to reduced adhesive effectiveness and diminished durability.
Several factors contribute to cohesive failure, including excessive joint movement, inadequate curing, and improper adhesive selection. To enhance the longevity and reliability of adhesives, these factors must be carefully controlled. In corrosion prevention strategies, cohesive properties should be considered as a critical parameter. Evaluating molecular consistency within adhesives applied to metallic surfaces is essential to ensure proper bonding and effective protective coating performance.
Now, let’s have a short discussion about the mechanism of cohesive failures.
Weak Boundary Layer Theory
The Weak Boundary Layer Theory suggests that bond failure at the interface primarily occurs due to the cohesive rupture of a weak boundary layer. In most cases, coating defects arise from the breakdown of this layer, which fails before the coating can form a strong adhesion with the substrate. Weak boundary layers can originate from various sources, including the coating itself, the substrate material, environmental factors, or a combination of these elements.
Several key factors contribute to the formation of weak boundary layers. One major cause is the development of corrosion or oxide layers on metal surfaces, which act as a barrier preventing strong adhesion. Additionally, low molecular weight compounds, such as release agents and plasticizers present on polymeric surfaces, can interfere with bonding. Another significant factor is the presence of impurities concentrated near the bonding interface, which can reduce adhesion strength and lead to premature detachment.
To prevent adhesion failure, weak boundary layers must be eliminated using physical or chemical surface treatments. Proper surface preparation ensures a strong bond between the coating and the substrate by removing any weak links that could contribute to early coating failure. Ensuring the integrity of the bonding interface is crucial for achieving durable and long-lasting adhesion.
Common Coating Defects and Their Causes
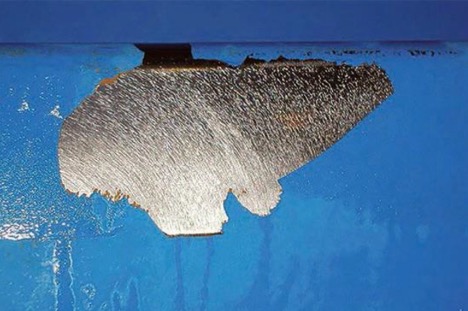
Coating defects refer to imperfections that arise during or after the application of a coating, affecting its appearance, performance, and durability. Let’s have a look at the major coating defects:
Blistering
Blistering occurs when a coated material is exposed to moisture, leading to the formation of dome-shaped defects on the surface. This phenomenon is primarily caused by the presence of water-soluble contaminants within or beneath the coating, which create localized pressure as moisture infiltrates. Additionally, rapid drying of the coating or exposure to harsh chemicals can contribute to blister formation by trapping volatile substances beneath the surface. Over time, these trapped materials expand, resulting in visible blisters that compromise the coating’s integrity and durability.
Peeling
Peeling is a defect characterized by the loss of adhesion between the paint film and the substrate or between different coating layers. This occurs when the bond strength weakens due to contaminants, surface irregularities, or incompatibility between coatings. Improper surface preparation, such as inadequate cleaning or priming, can also lead to peeling. In cases where different coating layers do not chemically or physically bond well, adhesion failure occurs, causing sections of the coating to detach.
Flaking
Flaking is a more severe form of peeling where large sections of the coating detach from the substrate, leaving exposed surfaces vulnerable to environmental damage. This defect is often caused by poor adhesion, excessive coating thickness, or degradation of the binder material over time. Flaking can significantly reduce the protective and aesthetic properties of a coating, leading to further deterioration and potential substrate damage.
Undercutting
Undercutting is a defect that occurs when corrosion develops beneath the coating, gradually pushing it away from the substrate. This typically happens at damaged or compromised areas of the coating, such as scratches or edges, where moisture and oxygen infiltrate. The resulting corrosion expands underneath the coating, causing it to lift and separate from the surface. Undercutting is particularly problematic in protective coatings used in industrial or marine environments, as it accelerates material degradation and compromises structural integrity.
Conclusion
Achieving strong adhesion in coatings is a combination of proper surface preparation, understanding adhesion mechanisms, and preventing common failures like peeling or blistering. Whether you’re dealing with paints, varnishes, or industrial coatings, ensuring the right balance of adhesion and cohesion is essential for long-term durability. The next time you apply a coating, remember—bonding matters!
References
https://pubs.acs.org/doi/10.1021/acs.langmuir.1c00047
https://coatings.specialchem.com/coatings-properties/adhesion
https://www.steeldata.info/macro/demo/data/3057.html
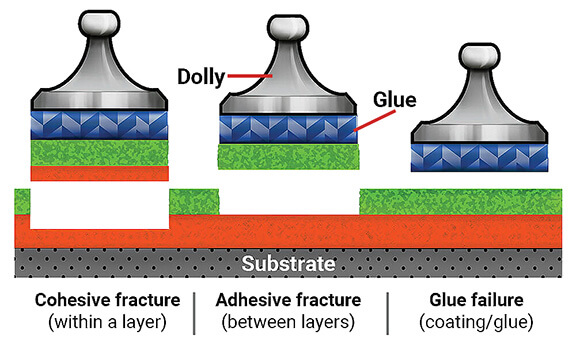
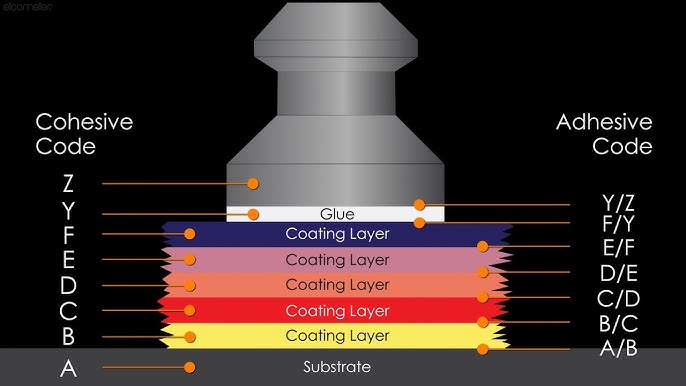

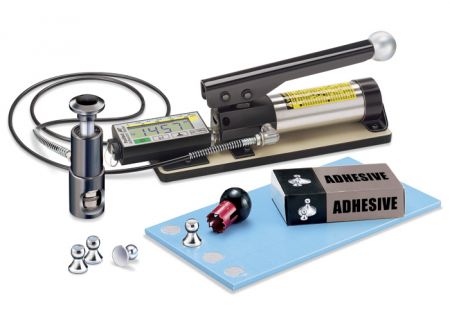
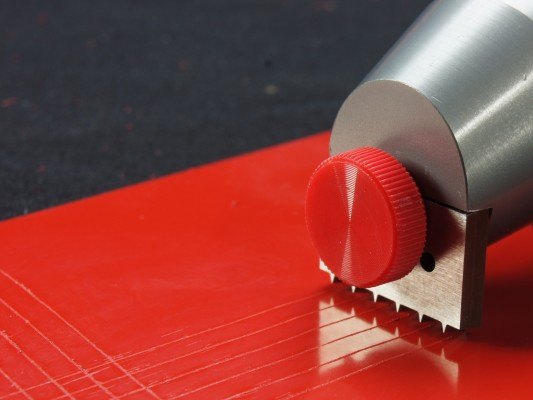
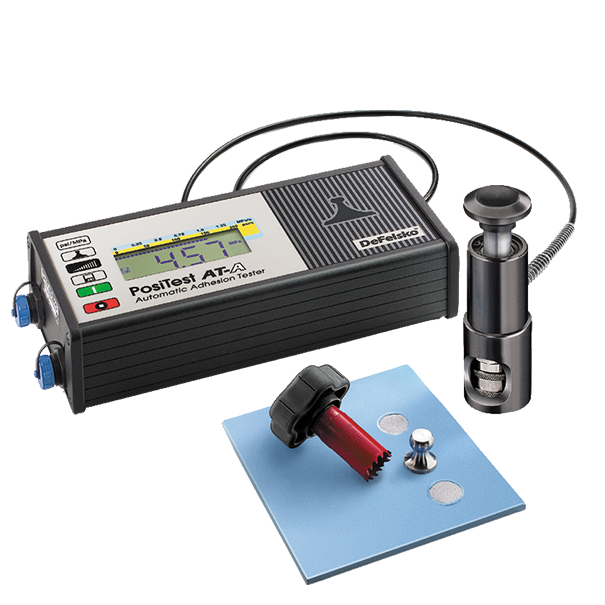