Comparative Table: Coating Properties
Compliance with Standards and Regulations
- Brushing
- Spraying
- Dipping (Dip Coating)
- Electroplating
- Chemical Vapor Deposition (CVD)
- Physical Vapor Deposition (PVD)
- Other Specialized Methods
Pull-Off Test (ASTM D4541, ISO 4624)
Electrochemical Impedance Spectroscopy (EIS)
Introduction
Protective coatings serve an important role in demanding industrial environments, where materials and structures are routinely exposed to harsh conditions such as chemical exposure, abrasion, UV radiation, high temperatures, and corrosive atmospheres. Protective coatings serve as a critical barrier to mitigate degradation, extending the service life and maintaining the functionality of assets. These coatings are tailored to withstand specific environmental stressors and mechanical demands, thereby reducing maintenance costs and operational downtime across a broad range of industries.
Let’s delve deeper into protective coatings, their types, properties and uses.
What are Protective Coatings?
Protective coatings are engineered layers applied to surfaces of substrates—typically metals, composites, or concrete—to prevent or reduce surface degradation from physical, chemical, and environmental factors. These coatings may serve multiple functions:
- Corrosion Resistance: Prevent electrochemical degradation in metals
- Chemical Protection: Provide resistance to acids, alkalis, and solvents
- Thermal Insulation: Shield against high or low temperatures
- Abrasion Resistance: Reduce wear from mechanical contact
- UV Protection: Inhibit photodegradation of underlying materials
- Aesthetic Improvement: Enhance appearance and identify equipment
Types of Protective Coatings
Organic Coatings
Organic coatings are polymer-based and form films that act as barriers. They are generally categorized into single-component and two-component systems.
Epoxies
- Composition: Bisphenol A or F-based resins, cured with amines or polyamides
- Properties: Excellent adhesion, chemical resistance, and mechanical strength
- Applications: Tank linings, offshore structures, pipeline coatings
- Limitations: Poor UV resistance; prone to chalking in sunlight
Polyurethanes
- Composition: Manufactured by reacting polyols with isocyanates
- Properties: High flexibility, abrasion resistance, UV stability
- Applications: Topcoats in automotive, aerospace, and infrastructure
- Limitations: Sensitive to moisture during curing
Acrylics
- Composition: Polymers or copolymers of acrylic acid derivatives
- Properties: Fast drying, good color retention, UV resistance
- Applications: Architectural coatings, decorative finishes, atmospheric exposure protection
- Limitations: Limited chemical resistance compared to epoxies
Inorganic Coatings
Inorganic coatings derive from silicates or ceramics and offer superior thermal and chemical resistance. They form crystalline or glassy matrices upon curing.
Silicate Coatings
- Composition: Alkali metal silicates (e.g., potassium silicate)
- Properties: High-temperature resistance, non-combustible, excellent adhesion to steel
- Applications: Chimney linings, heat exchangers, fire protection coatings
- Limitations: Brittle; poor flexibility
Ceramic Coatings
- Composition: Alumina, zirconia, titania-based systems
- Properties: Exceptional hardness, chemical resistance, thermal stability up to 1200°C
- Applications: Turbine blades, exhaust systems, aerospace components
- Limitations: Expensive and requires specialized application techniques (e.g., plasma spraying)
Metallic Coatings
Metallic coatings involve the application of a metal layer onto a substrate to provide sacrificial or barrier protection.
Galvanizing
- Process: Hot-dip coating of steel in molten zinc
- Protection Mechanism: Sacrificial (zinc corrodes preferentially to steel)
- Applications: Transmission towers, guardrails, rebar, outdoor structures
Thermal Spray Coatings
- Types: Flame spray, arc spray, plasma spray
- Materials: Zinc, aluminum, stainless steel, molybdenum
- Properties: Tailorable thickness, high bond strength, minimal heat distortion
- Applications: Jet engine components, marine structures, pipelines
- Limitations: Surface preparation critical; porosity may require sealing
Conversion Coatings
Conversion coatings chemically alter the surface of the substrate to form a protective compound that is integral to the surface.
Phosphate Coatings
- Process: Immersion in phosphoric acid solutions with zinc, manganese, or iron salts
- Properties: Good paint adhesion, moderate corrosion resistance
- Applications: Automotive underbodies, appliance housings
- Limitations: Require post-treatment with sealers or primers
Chromate Coatings
- Process: Treatment with hexavalent or trivalent chromium compounds
- Properties: Excellent corrosion resistance and paint adhesion
- Applications: Aerospace aluminum components, electronics
- Regulatory Note: Hexavalent chromium is restricted due to environmental and health concerns
Hybrid and Composite Coatings
These coatings integrate multiple chemistries or reinforcement phases to achieve superior multifunctional performance.
Epoxy-Polyurethane Hybrids
- Purpose: Combine chemical resistance (epoxy) with UV resistance (polyurethane)
- Applications: Protective topcoats for offshore and chemical plants
Nanocomposite Coatings
- Inclusions: SiO2, TiO2, graphene, or clay nanoparticles
- Properties: Enhanced barrier effect, scratch resistance, anti-microbial features
- Applications: Medical equipment, marine, and electronic enclosures
Ceramic-Polymer Composites
- Design: Dispersed ceramic fillers in a polymer matrix
- Properties: Improved thermal resistance, dielectric strength, and wear resistance
- Applications: Electrical insulation, aerospace thermal barriers
Comparative Table: Coating Properties
Coating Type | Corrosion Resistance | UV Stability | Temperature Resistance | Chemical Resistance | Typical Thickness (microns) |
Epoxy | High | Low | Up to 150°C | High | 150–300 |
Polyurethane | Moderate | High | Up to 120°C | Moderate | 50–100 |
Acrylic | Low to Moderate | High | Up to 90°C | Low | 30–60 |
Silicate | High | High | Up to 600°C | High | 50–200 |
Ceramic | Very High | High | Up to 1200°C | Very High | 100–400 |
Galvanizing | High (sacrificial) | Moderate | Up to 200°C | Moderate | >85 |
Thermal Spray | High | High | Up to 1000°C | High | 100–600 |
Phosphate | Moderate | Low | Up to 70°C | Low | 10–20 |
Chromate | High | Moderate | Up to 120°C | High | 0.5–5 |
Coating Functions
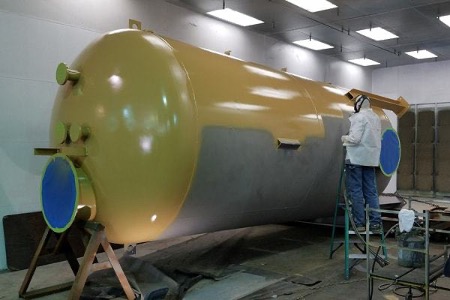
Corrosion Resistance
Corrosion is a predominant issue in industrial settings, particularly in environments involving moisture, salt, or aggressive chemicals. Protective coatings provide a physical barrier that isolates the substrate from corrosive agents. Common anti-corrosive coatings include:
- Zinc-rich primers: Act as sacrificial anodes, protecting steel through galvanic action.
- Epoxy coatings: Offer excellent adhesion and impermeability.
- Polyurethane topcoats: Provide additional UV resistance and mechanical strength.
Chemical Resistance
In chemical plants, storage tanks, and pipelines, resistance to acids, bases, solvents, and oxidizing agents is paramount. Coatings for chemical resistance include:
- Phenolic epoxies: Suitable for strong acids and solvents.
- Vinyl esters: Withstand aggressive chemicals like hydrochloric acid.
- Fluoropolymers (e.g., PTFE): Exhibit outstanding resistance across a wide pH range.
Thermal Protection
Industrial equipment often operates under high or fluctuating temperatures. Protective coatings in these scenarios must maintain integrity without degradation or loss of adhesion.
- Ceramic coatings: Resist temperatures above 1000°C.
- Silicone-based coatings: Maintain flexibility and adhesion at elevated temperatures.
- Aluminized coatings: Reflect radiant heat and provide oxidation resistance.
Wear and Abrasion Resistance
High wear applications, such as conveyors, chutes, and mining equipment, require coatings that can endure friction and particle impact.
- Polyurea and polyurethane coatings: Offer elastic recovery and abrasion resistance.
- Thermal spray coatings (e.g., WC-Co): Provide hard, wear-resistant surfaces.
- Epoxy-based systems with ceramic fillers: Improve erosion resistance.
UV and Weathering Protection
UV radiation and weathering can degrade polymeric materials, leading to chalking, color fading, and loss of mechanical properties. UV-resistant coatings extend service life in outdoor environments.
- Acrylic and polyurethane coatings: Resist photo-degradation and color loss.
- Fluoropolymer topcoats: Exhibit excellent long-term weathering resistance.
Coating Selection Criteria
Substrate Type
The nature of the substrate significantly influences coating selection. Different substrates require specific surface preparation and coating chemistry for proper adhesion and performance.
Substrate | Considerations | Recommended Coatings |
Carbon Steel | Prone to corrosion | Epoxy, zinc-rich primers, polyurethanes |
Stainless Steel | Passive oxide layer may reduce adhesion | Surface roughening, epoxy, fluoropolymers |
Aluminum | Oxidizes quickly, smooth surface | Conversion coatings, polyurethane |
Concrete | Porous, alkaline | Epoxy, polyurea, moisture-tolerant systems |
Environmental Exposure
Environmental exposure—chemical, marine, UV, temperature—dictates the type and complexity of protective systems.
- Chemical exposure: Demands coatings with specific chemical resistance (e.g., vinyl ester in acid tanks).
- Marine environments: Require multi-layer anti-corrosion systems with cathodic protection compatibility.
- High-temperature areas: Need thermally stable coatings (e.g., silicone or ceramic-based systems).
- Outdoor UV exposure: Must include UV-resistant topcoats like polyurethanes or fluoropolymers.
Mechanical Stresses
Mechanical loading, vibration, and impact require coatings that offer flexibility, toughness, or hardness depending on the type of stress.
- Abrasion resistance: Hard coatings like ceramic-filled epoxies or thermal spray systems.
- Impact resistance: Elastomeric coatings like polyurea.
- Flexural stress: Flexible polyurethane or epoxy formulations with elongation capacity.
Methods of Application
Let’s have a look at the different methods of applying coating to a substrate.
1. Brushing
In this method, liquid coatings—such as alkyds, epoxies, or polyurethanes—are applied manually using a brush or roller. It is best suited for projects involving limited surface area or when coating components with intricate geometries, such as joints, flanges, or weld seams, where control and precision are critical.
Brushing allows for relatively thick film builds per coat, which can be beneficial in achieving targeted dry film thickness (DFT) without multiple passes. However, because it relies heavily on the operator’s technique, uniformity across large areas is difficult to achieve.
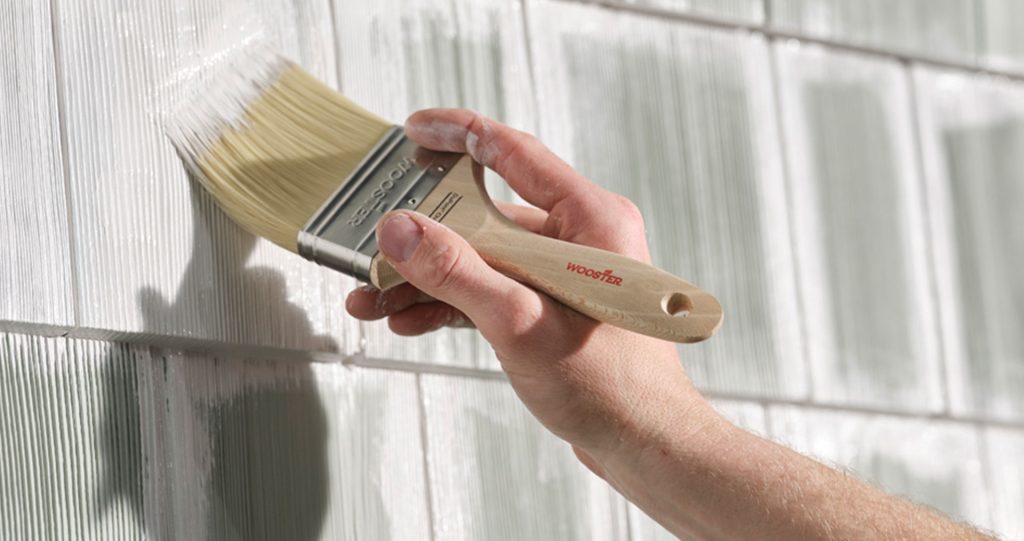
2. Spraying
Spray application is one of the most efficient and widely adopted methods in industrial coating operations due to its ability to deliver uniform, high-quality finishes over large areas with minimal manual effort. There are several spray technologies, including conventional air spray, airless spray, air-assisted airless, and electrostatic spray systems.
In conventional air spray, compressed air atomizes the coating material as it exits the spray nozzle, producing fine droplets for an even distribution. This method is suitable for low-viscosity coatings but can result in significant overspray and material loss. Airless spraying, on the other hand, forces high-viscosity coatings through a small orifice at high pressure (typically 1500–3000 psi), atomizing them without air assistance. This yields thicker films and better penetration, particularly on rough or profiled surfaces such as blasted steel.
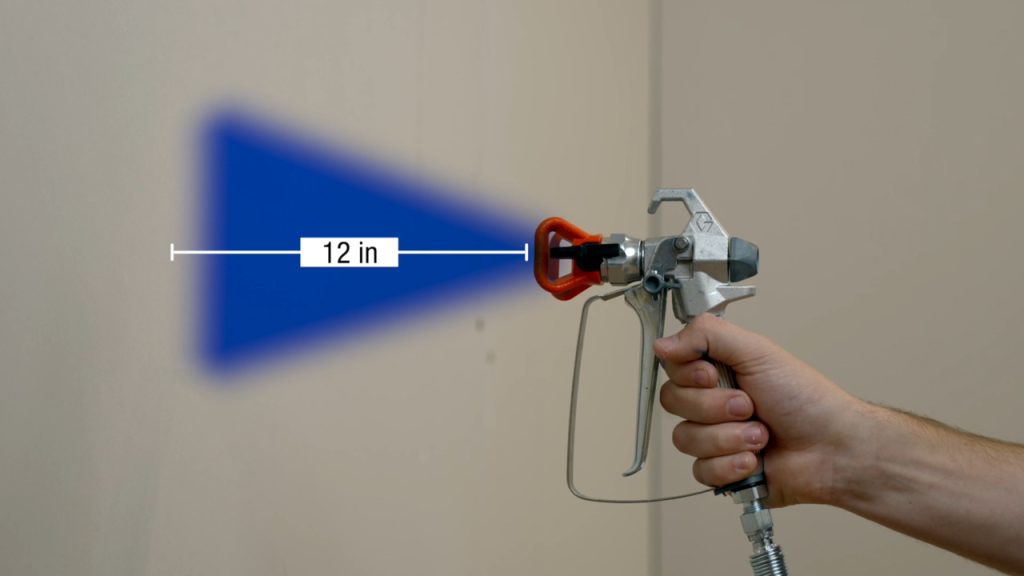
3. Dipping (Dip Coating)
Dip coating involves immersing the substrate into a tank containing the coating material and then withdrawing it at a controlled rate to allow excess material to drain off. The wet coating subsequently levels out by gravity and surface tension before being cured thermally or chemically.
This method is particularly useful for coating small, complex parts such as fasteners, threaded components, or tools, and is commonly employed in the application of corrosion-resistant coatings like zinc phosphate or epoxy primers. Dip coating provides 360-degree coverage, including internal recesses and difficult-to-reach geometries, which would be challenging for other techniques.
Film thickness is influenced by several parameters, including withdrawal speed, coating viscosity, and ambient conditions. Control over these factors is essential to achieving repeatable and uniform results. However, dip coating is not typically suited for very large or flat vertical surfaces due to the risk of sagging and pooling.
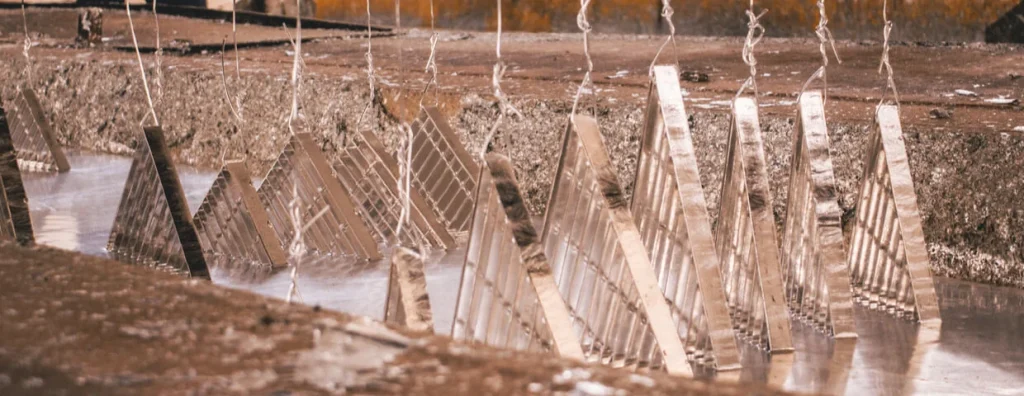
4. Electroplating
Electroplating is an electrochemical process where a metal coating is deposited onto a conductive substrate using an electric current. It is widely used to impart corrosion resistance, wear resistance, and decorative finish to metal components.
In a typical setup, the substrate (cathode) and the plating metal (anode) are submerged in an electrolyte solution containing metal ions. When a direct current is applied, metal cations reduce and deposit uniformly onto the substrate’s surface. Common electroplated metals include zinc, chromium, nickel, and cadmium, each selected based on desired performance characteristics.
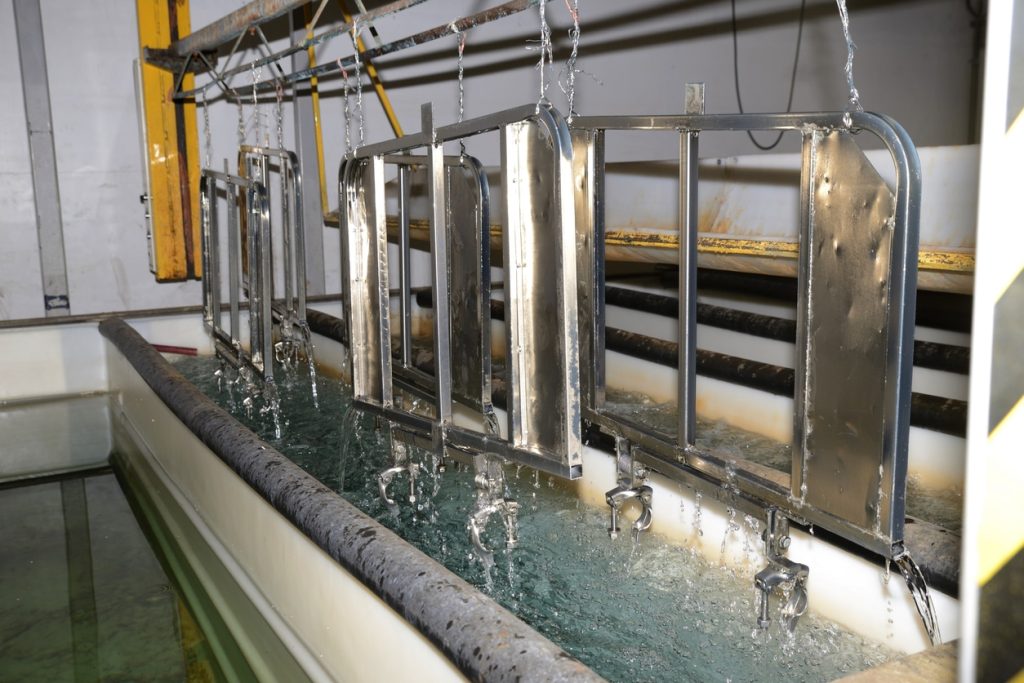
- Powder Coating
Powder coating is a solvent-free method that uses dry thermoplastic or thermosetting powders, applied electrostatically to a substrate and then cured under heat. The process typically involves three main stages: surface preparation, powder application using an electrostatic gun, and thermal curing in an oven.
The coating powder is charged as it exits the spray gun and is attracted to the grounded metal substrate, forming a uniform layer. The part is then subjected to elevated temperatures (typically 160–210°C) in a curing oven, where the powder melts, flows, and crosslinks to form a dense, adherent coating.
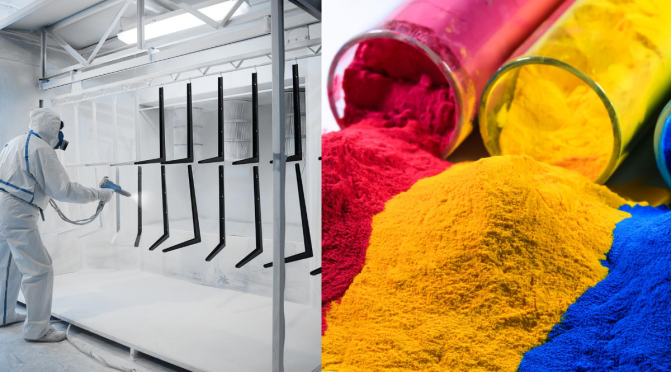
6. Chemical Vapor Deposition (CVD)
CVD is a high-performance, vapor-phase coating technique where gaseous reactants form a solid material on a heated substrate through chemical reactions. It is commonly used to deposit ultra-thin films with excellent conformity and adhesion, even on complex geometries.
During CVD, precursors such as metal chlorides or organometallic compounds are introduced into a reaction chamber containing the substrate, which is maintained at elevated temperatures (typically 400–1200°C). The reactants decompose or react near the hot surface, forming a thin film of material—such as silicon carbide, titanium nitride, or alumina—while volatile byproducts are removed via exhaust.
CVD coatings offer exceptional hardness, corrosion resistance, and thermal stability. This makes them invaluable in semiconductor fabrication, cutting tools, aerospace turbine blades, and biomedical implants. However, CVD requires high capital investment, careful control of process chemistry, and strict safety measures due to toxic or pyrophoric gases.
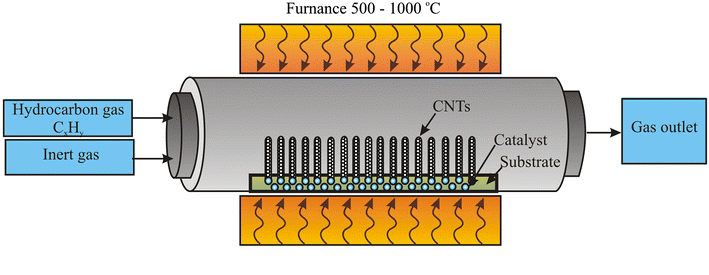
7. Physical Vapor Deposition (PVD)
PVD is another vacuum-based technique where the coating material is physically vaporized—through thermal evaporation, sputtering, or arc vaporization—and then condensed onto the substrate surface to form a thin, dense film.
In sputtering, for instance, a target material is bombarded with high-energy ions (usually argon), ejecting atoms that then deposit on the substrate. PVD coatings are typically applied at lower substrate temperatures (150–500°C) compared to CVD, allowing for use on temperature-sensitive substrates.
Common PVD coatings include titanium nitride (TiN), chromium nitride (CrN), and DLC (diamond-like carbon), offering high hardness, low friction, and aesthetic finishes. Applications include tooling, medical devices, optical components, and microelectronics.
Compared to CVD, PVD provides better control over layer thickness and composition, but adhesion may be more sensitive to surface contamination or roughness. Pre-treatment like ion cleaning or plasma etching is often used to enhance performance.
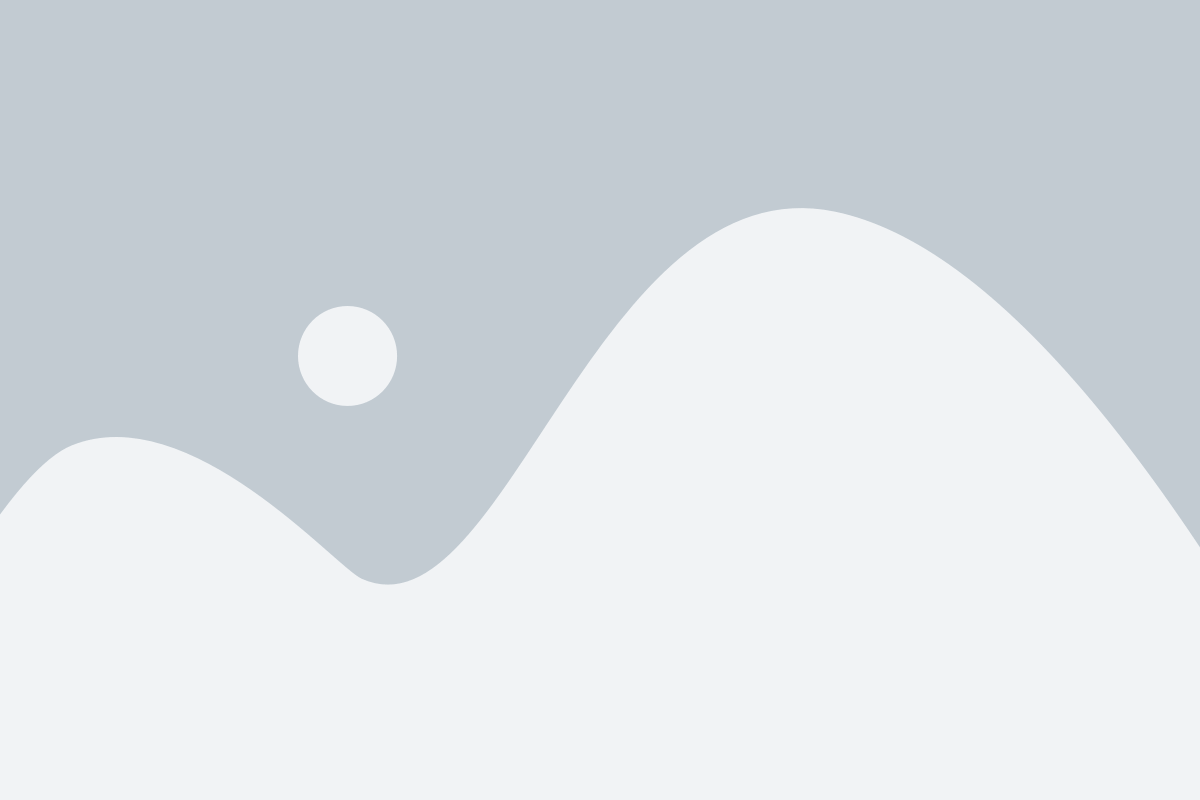
8. Other Specialized Methods
Beyond the main techniques listed above, several niche or hybrid methods exist for applying protective coatings:
- Thermal Spray Coating: Involves melting metal or ceramic powders and propelling them onto a substrate using a high-velocity gas stream. Used for wear-resistant and thermal barrier coatings in aerospace and energy sectors.
- Anodizing: An electrochemical passivation process for aluminum and magnesium that forms a protective oxide layer. Often used for corrosion resistance and aesthetic enhancement.
- Hot-Dip Galvanizing: A method where steel is immersed in molten zinc to form a metallurgically bonded coating. Suitable for large structural elements like guardrails, bridges, and transmission towers.
L
Performance Testing and Evaluation of Protective Coatings
Let’s have a look at the different testing procedures used to evaluate the performance of protective coatings.
Adhesion Testing
Adhesion is the fundamental property that determines how well a coating remains bonded to the substrate under operational stresses. Poor adhesion leads to delamination, blistering, or flaking—resulting in localized corrosion and eventual system failure.
Cross-Cut Test (ASTM D3359, ISO 2409)
In this method, a lattice pattern of cuts is made through the coating to the substrate using a multi-blade cutter. Adhesive tape is then applied and pulled away at a consistent angle and speed. The degree of coating removal is rated on a numerical scale, with lower numbers indicating better adhesion. It is best suited for coatings up to 250 µm thick and on flat, rigid substrates.
Pull-Off Test (ASTM D4541, ISO 4624)
The pull-off test provides a quantitative measure of adhesion strength. A loading fixture (dolly) is glued to the coating surface using an epoxy adhesive. After curing, the dolly is pulled perpendicularly using a hydraulic or pneumatic adhesion tester. The force at which the coating detaches is recorded in megapascals (MPa).
This method is suitable for laboratory evaluations and forensic failure analysis. Results can vary depending on the type of failure—cohesive (within the coating), adhesive (interface failure), or substrate failure.
Adhesion Performance Benchmarks
Coating Type | Typical Adhesion (Pull-Off) | Industry Application |
Epoxy Primer | 5–10 MPa | Marine, Oil & Gas |
Polyurethane | 3–8 MPa | Infrastructure, Automotive |
Zinc-Rich Primer | 4–7 MPa | Structural Steel, Offshore |
Thermal Spray Zn | 6–10 MPa | Bridges, Coastal Infrastructure |
Salt Spray (Fog) Testing
Salt spray testing, as described in ASTM B117 and ISO 9227, is a widely used accelerated corrosion test that simulates marine or coastal environments. Coated panels are placed in a test chamber maintained at 35°C and continuously exposed to a fine mist of 5% NaCl solution.
This test primarily assesses the corrosion resistance of the entire coating system, including any sacrificial elements like zinc primers. It also reveals failure modes such as underfilm corrosion, blistering, or edge creepage.
The performance of coatings in salt spray is highly dependent on surface preparation, primer selection, and coating thickness. For instance, a three-coat system (zinc primer + epoxy + polyurethane) typically withstands 2000+ hours with minimal scribe creep (<2 mm).
Electrochemical Impedance Spectroscopy (EIS)
Electrochemical Impedance Spectroscopy is a non-destructive, highly sensitive technique that characterizes the barrier properties of coatings by measuring their impedance across a range of AC frequencies. It provides information about coating integrity, water uptake, and defect formation long before visual degradation appears.
The sample is immersed in an electrolyte (e.g., 3.5% NaCl) and subjected to a small AC voltage (typically 10 mV) across frequencies ranging from 100 kHz to 10 mHz.
The impedance response is plotted as a Bode or Nyquist plot and modeled using equivalent electrical circuits representing coating resistance (Rc), pore resistance (Rp), and double-layer capacitance (Cdl).
High total impedance (>10⁸ ohm·cm²) at low frequency (0.1 Hz) is indicative of an excellent barrier coating. As coatings degrade, impedance decreases due to electrolyte ingress and pore formation. EIS is highly sensitive to detecting early-stage degradation and water uptake in coatings, often before visible signs of deterioration appear. This sensitivity makes EIS particularly valuable for predictive maintenance and longevity assessments of protective coatings.
Accelerated Weathering Tests
Accelerated weathering simulates long-term environmental exposure in condensed timeframes. Coatings are subjected to cycles of UV radiation, moisture, heat, and sometimes salt or pollutants to predict how they will perform over years of outdoor exposure.
The primary standards include:
- ASTM G154 (fluorescent UV exposure)
- ASTM G155 (xenon arc exposure)
- ISO 11507, ISO 11341
In UV fluorescent tests (QUV testers), samples are exposed to UV-A or UV-B light combined with condensation or water spray cycles at controlled temperatures. Xenon arc testing offers a broader spectral simulation of natural sunlight and can include temperature and humidity control. Total exposure can last from 500 to 5000 hours, depending on durability requirements.
Evaluation Parameters
- Gloss retention (ASTM D523)
- Color change (ΔE) (ASTM D2244)
- Chalking (ASTM D4214)
- Cracking or flaking
- Loss of adhesion
These metrics help determine how well a coating retains aesthetic and functional performance when exposed to environmental stressors such as UV degradation and hydrolysis.
Mechanical Durability Tests
Mechanical durability refers to the coating’s resistance to abrasion, impact, and deformation during service. Such properties are critical in applications involving physical contact, particulate erosion, or vibration.
Abrasion Resistance (ASTM D4060)
This test uses a Taber Abraser equipped with rotating abrasive wheels under a fixed load. The coated sample is subjected to a predefined number of cycles (e.g., 1000) and the weight loss is measured.
Materials like epoxy-polyester hybrids and fluoropolymer coatings show high abrasion resistance with <50 mg weight loss over 1000 cycles.
Impact Resistance (ASTM D2794)
A known weight is dropped from a specific height onto the coated surface using a falling dart apparatus. The coating is evaluated for cracking, chipping, or delamination. Impact resistance is especially critical in transportation, pipelines, and structural components exposed to shock or mechanical loading.
Conclusion
Protective coatings play a vital role in extending the lifespan and reliability of materials exposed to harsh industrial environments. By selecting the appropriate coating type based on substrate characteristics, environmental exposure, and performance requirements, engineers can significantly reduce maintenance costs, prevent failure, and ensure regulatory compliance. As material science advances, hybrid and smart coatings are poised to offer even greater functionality, marking the future of surface protection technology.
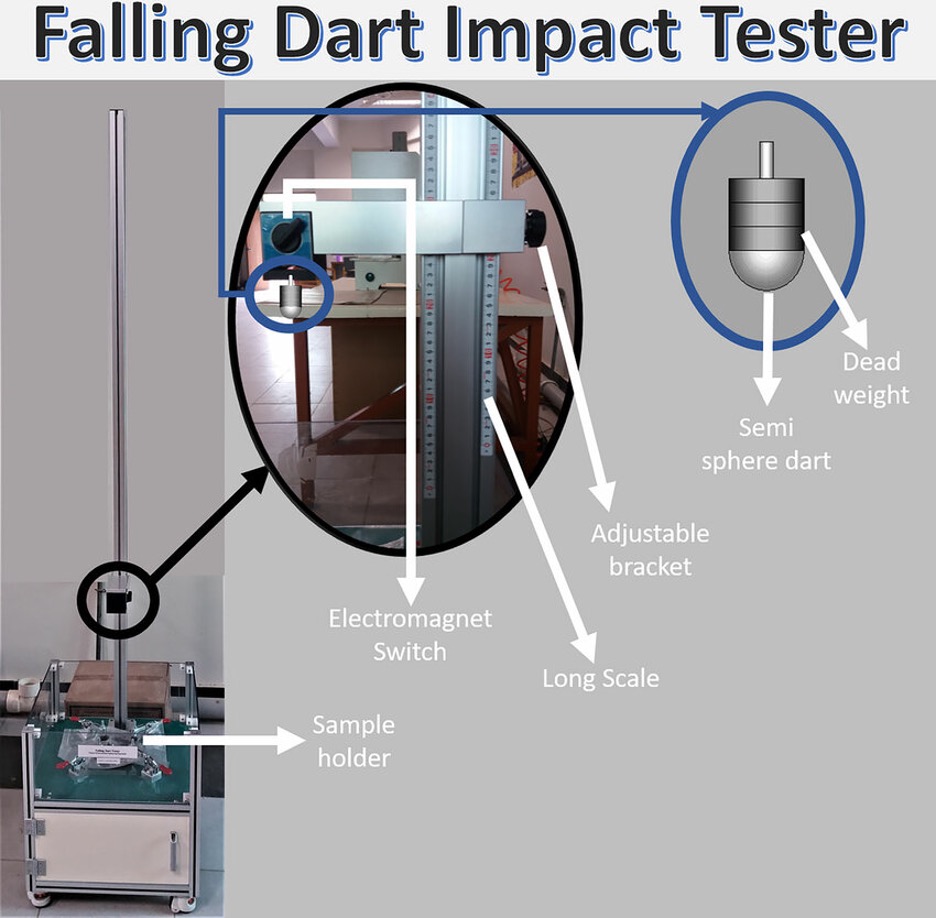