Introduction
Thermal spray coating is a surface engineering process that involves the deposition of fine particles, melted or semi-melted, propelled at high velocities onto a prepared substrate to form a protective or functional layer. This process is known for its versatility, enabling the application of metallic, ceramic, and polymeric materials onto diverse substrates. This capability has positioned thermal spray coating as a crucial technology in sectors such as aerospace, automotive, energy, biomedical, and heavy machinery.
What is Thermal Spray Coating?
Thermal spraying is a surface coating technique used in industrial applications, where materials in a heated or molten state are propelled at high speed onto a surface to form a protective layer. This process accommodates a wide range of materials—including metals, ceramics, cermets, and polymers—and is commonly used to improve resistance to wear, corrosion, and high temperatures.
The process relies on energy sources such as electric arcs or high-temperature combustion to heat powdered feedstock materials. These materials are then sprayed onto a substrate, where they flatten into thin discs known as “splats” or “platelets.” As these particles overlap and solidify, they form dense, durable coatings that typically range in thickness from 0.1 mm to 10 mm. The technique is highly adaptable, as virtually any material that can melt or become pliable during spraying can be applied.
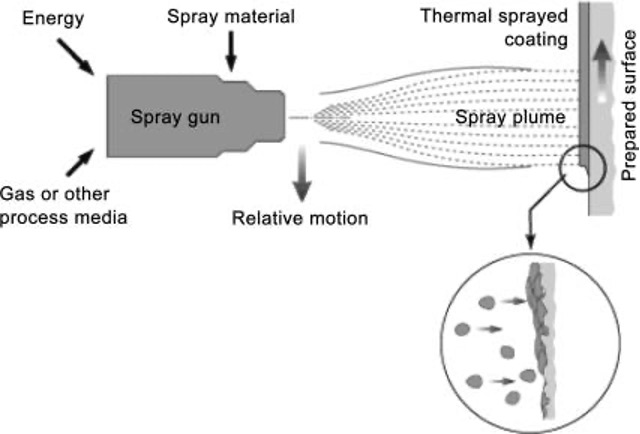
Importance of Thermal Spray Coating
The increasing demand for improved wear resistance, corrosion protection, thermal barrier properties, and electrical insulation or conductivity in high-performance components has driven the adoption of thermal spray technologies. Components such as turbine blades, biomedical implants, hydraulic pistons, and electronic components often rely on thermal spray coatings to extend service life and maintain performance under extreme operating conditions. The industrial relevance of thermal spray coatings is governed by standards such as ASTM C633 for adhesion strength and ISO 14918 for qualification of thermal sprayers, which ensure the reproducibility and quality of the coatings.
Types of Thermal Spraying
Flame Spraying
Flame spraying is one of the earliest thermal spray techniques and involves the use of a combustible gas, typically acetylene or propane, as the heat source. The feedstock material, usually in wire or powder form, is melted in the flame and atomized by compressed air before being propelled onto the substrate. The process operates at relatively low particle velocities and moderate temperatures, generally in the range of 2,500 to 3,000 K.
Due to its simplicity and cost-effectiveness, flame spraying remains widely used for applying corrosion-resistant coatings, particularly zinc and aluminum, on steel structures. The coatings tend to be more porous and less dense compared to other thermal spray methods, making post-treatment such as sealing necessary in many applications.
Although suitable for large surface areas and onsite applications, flame spraying has limitations in terms of coating density, bond strength, and oxide content.
Arc Spraying
Arc spraying utilizes two consumable metallic wires that are electrically charged to form an arc at their contact point. The arc melts the wire tips, and a high-velocity stream of compressed air or inert gas atomizes and propels the molten droplets onto the substrate. The process is typically operated at voltages between 28 to 40 V and currents from 100 to 600 A.
This method is particularly efficient in terms of material deposition rate and is often used for applying zinc, aluminum, and steel coatings for corrosion protection.The arc spray process produces coatings with better mechanical properties and adhesion than flame-sprayed coatings, albeit with slightly higher equipment costs.
The key advantages of arc spraying include high productivity, good bond strength, and the ability to coat large areas economically. However, the process is generally limited to electrically conductive feedstocks and can result in high porosity if not properly controlled.
Plasma Spraying
Plasma spraying is a high-temperature process utilizing a plasma torch to generate a jet of ionized gas, reaching temperatures exceeding 15,000 K. Feedstock in powder form is introduced into the plasma plume, where it melts and is accelerated toward the substrate. The process is often carried out in atmospheric conditions (APS), but for critical applications, it can also be performed in controlled environments such as vacuum plasma spray (VPS) or low-pressure plasma spray (LPPS).
This method offers excellent control over coating microstructure and is capable of depositing high-melting-point materials, including ceramics like zirconia, alumina, and chromium oxide. Plasma spraying is widely used in aerospace for thermal barrier coatings (TBCs) on turbine blades, as well as in biomedical applications for hydroxyapatite coatings on implants.
However, plasma spraying requires sophisticated equipment, precise process control, and skilled operators. Its complexity and cost are justified by the performance of the resulting coatings, which exhibit low porosity, high bond strength, and excellent thermal resistance.
The HVOF process is characterized by the combustion of oxygen and fuel gases (such as propane, hydrogen, or kerosene) at high pressure in a combustion chamber to produce a high-velocity exhaust stream. This stream accelerates the powder particles to velocities approaching Mach 2, while maintaining moderate temperatures that prevent excessive oxidation or decomposition of the feedstock.
HVOF coatings are known for their high density, low oxide content, and superior bond strength. Typical coating materials include tungsten carbide-cobalt (WC-Co), chromium carbide-nickel chromium (CrC-NiCr), and stainless steel alloys. These coatings are extensively employed in aerospace, petrochemical, and mining industries where wear and corrosion resistance are critical.
Process parameters such as fuel-to-oxygen ratio, standoff distance, and powder feed rate are crucial for optimizing coating properties. ASTM C633 and ISO 14924 are often used to evaluate adhesion and quality of HVOF coatings. Despite the high capital investment and operational complexity, the HVOF process remains a preferred method for critical applications requiring robust, long-lasting coatings.
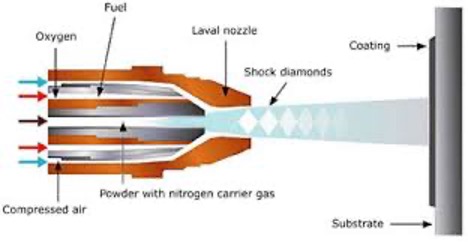
Cold Spraying
Cold spray is a unique thermal spray technique that operates without melting the feedstock. Instead, powdered materials are accelerated to supersonic velocities (typically >500 m/s) using compressed gas (helium or nitrogen) and impact the substrate at high kinetic energy. The bonding mechanism relies on severe plastic deformation and localized mechanical interlocking, making it a solid-state process.
This method is particularly advantageous for materials sensitive to oxidation, such as copper, aluminum, and titanium. Cold spray is gaining prominence in additive manufacturing, structural repair, and electronics due to its ability to produce dense, oxide-free coatings with minimal thermal distortion.
Cold spray coatings are evaluated using standards such as ASTM C1866, which outlines procedures for assessing the physical and mechanical properties of such deposits. The primary limitation of cold spray is its ineffectiveness for hard or brittle materials, which require higher temperatures for proper deposition. Nevertheless, its low-heat input, environmental friendliness, and high deposition efficiency make it an increasingly attractive option.
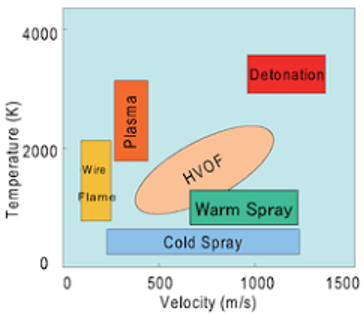
Process | Heat Source | Velocity | Key Features |
Flame Spray | Combustion flame | Low | Simple, low cost, used for corrosion protection |
Arc Spray | Electric arc | Medium | High deposition rate, for Zn/Al coatings |
Plasma Spray | Ionized gas (plasma) | Medium | For ceramics and high-melting-point materials |
HVOF (High-Velocity Oxy-Fuel) | Combustion (high pressure) | High | Dense, strong coatings (e.g., WC-Co) |
Cold Spray | Compressed gas (no melting) | Very High | Minimal oxidation, good for soft metals |
Materials Used in Thermal Spraying
The selection of feedstock material in thermal spraying is governed by the intended function of the coating, service environment, and compatibility with the chosen spray process. Coating materials are typically engineered to meet performance metrics such as hardness, corrosion resistance, oxidation stability, thermal conductivity or insulation, and wear behavior. These materials are generally categorized into metals, ceramics, carbides, and cermets, each offering distinct microstructural and thermophysical characteristics.
Metallic Coatings
Metals are frequently used in thermal spray applications for corrosion protection, dimensional restoration, and electrical functionality. Common metallic feedstocks include aluminum, zinc, copper, molybdenum, and stainless steels. For example, zinc and aluminum—applied via arc or flame spraying—are extensively used in marine and infrastructure sectors as sacrificial anodes to protect steel substrates. Aluminum-bronze and molybdenum are often used in bearing surfaces and wear-resistant overlays.
In high-temperature environments, nickel-based alloys such as NiCr and Inconel (e.g., 625, 718) are preferred due to their oxidation and creep resistance. These are frequently deposited via HVOF or plasma spray, particularly in aerospace and power generation turbines. The selection and qualification of metallic feedstock are governed by standards such as ISO 14923, which outlines coating properties for metallic and other inorganic coatings.
Ceramic Coatings
Ceramics are widely employed in thermal barrier coatings (TBCs), dielectric layers, and chemically inert barriers. Their high melting points, thermal stability, and resistance to corrosive environments make them suitable for high-temperature and chemically aggressive applications. Plasma spraying is typically used due to the elevated temperatures required for ceramic melting.
The most widely used ceramic in thermal spraying is yttria-stabilized zirconia (YSZ), which serves as the topcoat in TBC systems. Other ceramics include alumina (Al₂O₃), titania (TiO₂), and spinel compounds, used for dielectric or wear-resistant purposes. Hydroxyapatite (Ca₁₀(PO₄)₆(OH)₂) coatings, applied on orthopedic implants via plasma spraying, enhance osseointegration and biocompatibility.
Carbides and Cermets
Carbides are employed for their exceptional hardness and abrasion resistance. Tungsten carbide (WC) and chromium carbide (Cr₃C₂) are the most prevalent, typically incorporated into a ductile metal matrix such as cobalt (Co), nickel (Ni), or chromium (Cr) to form a cermet (ceramic-metal composite). The resulting material combines ceramic hardness with metallic toughness, allowing it to withstand extreme tribological conditions.
WC-Co coatings, when deposited via HVOF, offer high wear resistance, low porosity, and excellent bond strength. They are common in oil & gas, mining, and aerospace industries for critical wear components such as gate valves, landing gear, and pump sleeves. Chromium carbide-based coatings are preferred for high-temperature applications, due to their superior oxidation resistance compared to WC-based coatings.
Selection of the appropriate carbide or cermet system must consider the thermal spray process compatibility, phase stability (e.g., prevention of WC decomposition at high temperatures), and service environment. ISO 14920 provides guidelines on the preparation of test specimens and evaluation of sprayed cermet coatings, while standards such as ASTM B946 define properties of thermally sprayed WC-based materials.
Next, we move on to the surface preparation and post-treatment processes.
Surface Preparation and Post-Treatment Processes
The functional integrity of a thermal spray coating is critically dependent on the condition of the substrate prior to deposition and the post-processing treatment following deposition. These peripheral steps are not secondary but very crucial to achieving coating adhesion, durability, and consistent performance under service conditions.
Surface Preparation
Effective surface preparation is vital for promoting mechanical interlocking and metallurgical bonding between the coating and the substrate. The standard method for surface preparation is abrasive blasting, typically using alumina or steel grit to achieve a surface roughness (Ra) in the range of 3.5 to 6.5 µm, depending on the coating system. The objective is to remove surface oxides, contaminants, and mill scale while creating a controlled anchor profile.
ASTM D7127 specifies procedures for measuring surface roughness of substrates intended for thermal spray applications, while ISO 8503-2 offers standards for visual assessment of surface profiles. Surface preparation must be tailored to the coating type—carbide coatings may require a more aggressive profile than metallic overlays, for instance.
In addition to mechanical cleaning, degreasing with solvents or alkaline solutions is employed to eliminate oils and moisture that could impair coating adhesion. The use of masking materials (ceramic tapes, silicone sheets, or metallic fixtures) is also crucial when coating complex geometries or protecting non-target areas.
Post-Treatment Processes
Once the coating is deposited, several post-treatment steps may be implemented to improve surface finish, mechanical integrity, and functional performance. These include:
Heat Treatment: Some coatings—especially those with residual stress or phase instability—benefit from post-spray heat treatment. For example, WC-Co coatings may undergo stress relief annealing at 300–500 °C, while plasma-sprayed ceramic coatings can be sintered at elevated temperatures to reduce porosity.
Sealing: Porous coatings, particularly those applied via flame or arc spraying, are often sealed with organic or inorganic sealants to improve corrosion resistance and reduce permeability. ASTM D7366 outlines standard test methods for evaluating the sealing performance of thermally sprayed coatings.
Machining and Grinding: Thermal spray coatings frequently require finishing operations to meet dimensional tolerances or surface roughness criteria. Hard coatings such as carbides are typically finished via diamond grinding, whereas metallic overlays may be machined using conventional tools.
Shot Peening and Residual Stress Management: In high-cycle fatigue environments, residual tensile stresses in the coating or substrate may lead to premature failure. Shot peening can be used to induce beneficial compressive stresses, enhancing fatigue performance.
Non-Destructive Testing (NDT): Inspection methods such as eddy current testing, ultrasonic inspection, and metallographic analysis are utilized for quality assurance. ISO 14924 and ISO 22826 provide procedures for destructive and non-destructive testing of sprayed coatings.
Let’s now examine the performance metrics that define the suitability of thermal spray coatings, followed by the non-destructive testing (NDT) methods used for quality assurance and life-cycle monitoring.
Coating Performance Metrics
The effectiveness of a thermal spray coating is judged not only by its initial appearance or deposition efficiency but by how well it performs under specific service conditions. Coating performance is evaluated through a combination of mechanical, physical, and functional properties—each closely tied to the microstructure and integrity of the coating-substrate interface. These metrics must be quantitatively characterized to meet application-specific requirements and regulatory standards.
Adhesion Strength
Adhesion strength is one of the most critical parameters in assessing coating performance. It represents the bonding quality between the coating and substrate, typically governed by mechanical interlocking, chemical bonding, and residual stress states. Adhesion is commonly quantified via tensile pull-off testing as per ASTM C633, which involves bonding the coated surface to a fixture using a high-strength adhesive and applying axial tensile load until failure. Adhesion strengths of >50 MPa are common for plasma and HVOF coatings, while lower values are typical for arc or flame-sprayed systems.
Hardness and Wear Resistance
Coating hardness is closely linked to wear resistance, particularly for applications involving abrasion, erosion, or fretting. Hardness is usually measured using microhardness testers under low loads (100–500 g) in accordance with ASTM E384or ISO 4516. Hard coatings such as WC-Co can achieve Vickers hardness values exceeding 1,000 HV₀.₃, while ceramic coatings like Al₂O₃ may approach similar values depending on porosity and grain structure.
Tribological performance can be assessed through ASTM G65 (dry sand rubber wheel test) or ASTM G99 (pin-on-disk), providing metrics such as wear rate (volume loss per unit load and distance). These help quantify coating integrity under simulated service conditions.
Porosity and Density
Porosity impacts both mechanical properties and environmental resistance. Low porosity (<1–2%) is essential in barrier coatings intended to prevent ingress of corrosive species or gases. Porosity is generally quantified through image analysis of polished cross-sections as per ASTM E2109, which provides methods for determining volume percent porosity from optical micrographs or scanning electron microscopy (SEM).
Density, a related parameter, is evaluated using Archimedes’ principle (ASTM B311) or calculated from coating mass and volume measurements. Dense coatings like those from HVOF exhibit near-theoretical density and minimal interlamellar voids, contributing to high performance under mechanical and thermal loads.
Residual Stress and Strain Behavior
Thermal spray processes inherently induce residual stresses due to rapid solidification and thermal gradients. Tensile residual stresses can compromise coating adhesion and fatigue life, while compressive stresses may improve resistance to crack initiation. X-ray diffraction (XRD) and hole-drilling methods, per ASTM E837 or ISO 21432, are used for residual stress measurement.
Coatings subjected to cyclic mechanical or thermal loading are also assessed for their strain accommodation behavior. This is particularly important in TBCs where thermal expansion mismatch between layers can cause delamination.
Corrosion and Oxidation Resistance
Coatings exposed to corrosive or oxidizing environments are evaluated using electrochemical tests such as potentiodynamic polarization (ASTM G59), electrochemical impedance spectroscopy (EIS), and salt spray testing (ASTM B117). These tests help assess the integrity of metallic and ceramic barriers in aggressive environments, such as marine, offshore, or chemical processing conditions.
Coatings based on Al, Zn, or Cr-carbides, or those incorporating rare earth oxides, are particularly resistant to oxidation and chlorination. Thermogravimetric analysis (TGA) is often used to determine oxidation kinetics at elevated temperatures.
Non-Destructive Testing (NDT) Methods for Thermal Spray Coatings
Non-destructive testing is indispensable for verifying coating quality, detecting subsurface defects, and ensuring compliance with industrial specifications without compromising component integrity. The diversity of thermal spray applications requires a broad toolkit of NDT methods, each suited for detecting specific flaws such as delaminations, porosity, cracking, or thickness inconsistencies.
Ultrasonic Testing (UT)
Ultrasonic inspection is widely used for thickness measurement, delamination detection, and bond integrity evaluation. Pulsed echo techniques can detect variations in acoustic impedance between the coating and substrate, revealing disbonds or internal voids. High-frequency UT probes (typically 10–25 MHz) are required due to the thin and dense nature of thermal spray coatings.
Time-of-flight techniques and C-scan imaging further enhance defect localization. ASTM E2375 and ISO 16811 outline the procedures for ultrasonic examination of thermal spray and other surface coatings.
Eddy Current Testing (ECT)
Eddy current testing is effective for evaluating coating thickness and surface discontinuities, particularly in electrically conductive coatings. It is especially useful for detecting localized variations or micro-cracks in metallic overlays such as NiCr or Al-based systems. ASTM E376 provides standards for eddy current thickness measurements, while ISO 21968 addresses flaw detection.
ECT is non-contact and fast, making it suitable for in-line inspection of large components such as aircraft panels, rotors, or turbine blades.
Infrared Thermography
Active thermography, including pulsed and lock-in modes, is used to detect sub-surface disbonds and cracks by observing transient or steady-state thermal patterns after stimulation. Defects disrupt heat flow, creating anomalies in the thermal image. This technique is particularly effective for low-conductivity coatings like ceramics or for inspecting layered structures.
Thermographic inspection conforms to standards like ASTM E2582, which specifies procedures for active thermographic evaluation.
X-ray and Radiographic Testing
Digital radiography and computed tomography (CT) enable high-resolution visualization of internal coating features, including pores, inclusions, and delaminations. These methods are particularly useful for thick or multilayered coatings where surface inspection is insufficient.
X-ray inspection requires high contrast resolution and calibrated exposure parameters. While not always suitable for field applications, it is invaluable for aerospace and nuclear-grade components where defect tolerance is minimal.
Acoustic Emission (AE) and Laser Shearography
Advanced NDT methods such as AE and shearography are employed in specialized applications. AE detects transient elastic waves from crack initiation or growth during mechanical loading, while shearography uses laser interferometry to visualize strain-induced surface deformation. Both methods can detect early-stage delamination or cracking in service-loaded coatings.
Conclusion
Thermal spray coating is a vital surface engineering technology offering tailored protection against wear, corrosion, and high temperatures. Through precise process control, material selection, and rigorous testing, it ensures enhanced performance and longevity of components across industries. Its versatility continues to expand with advancements in materials and deposition techniques.
Prepared by:
R. Venkatesan
Protective Coating Specialist
FROSIO / ICorr Lead Trainer
HTS EDUCATION AND DEVELOPMENT LLC (Dubai)
HTS COATING FZC (Sharjah)
HARVISH TECHNICAL SERVICES (India)