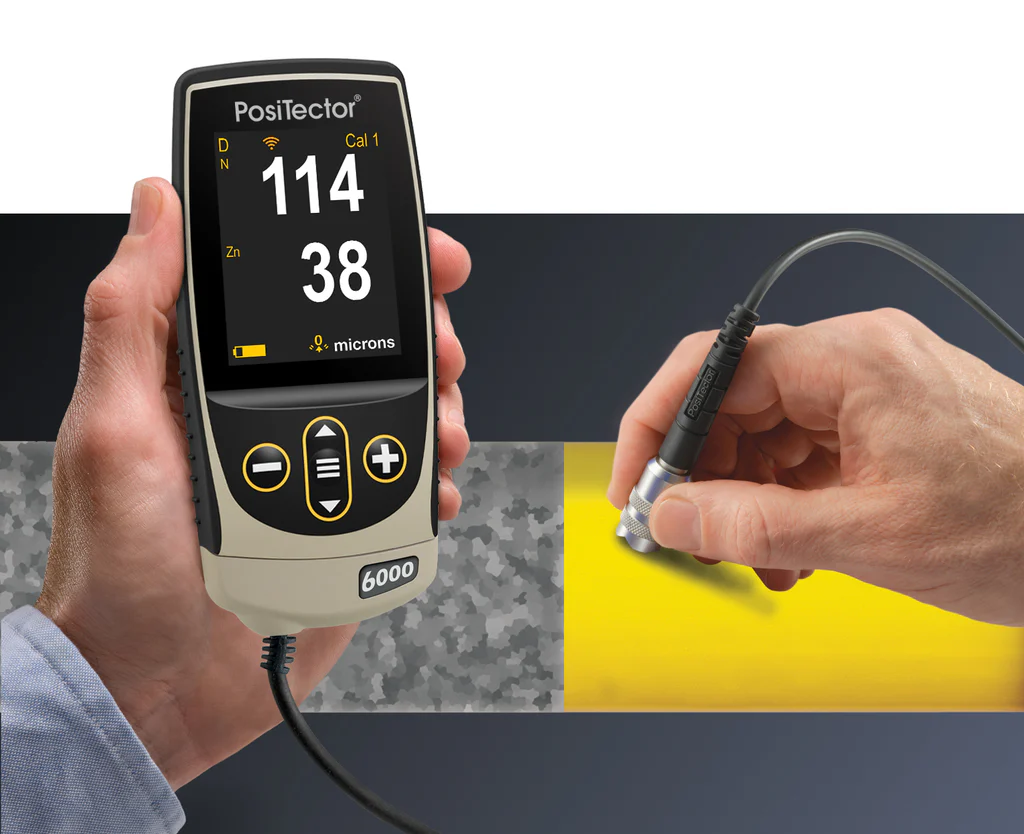
Who is Coating or Painting Inspector?
Simple Definition:
Any contracted person having responsibilities (Trained & Certified) to carry out the coating Inspection activities according to the project specific requirements.
OR
A Coating or Painting Inspector is an indispensable asset to any project involving coating applications. This role is fulfilled by a contracted professional who brings both training and certification to the table, ensuring that all coating inspection activities are conducted with precision and expertise.
These inspectors are responsible for carrying out inspections that align with the specific requirements of each project. Their attention to detail and adherence to standards guarantee that the coatings applied meet all necessary criteria, thereby contributing significantly to the quality and longevity of our work.
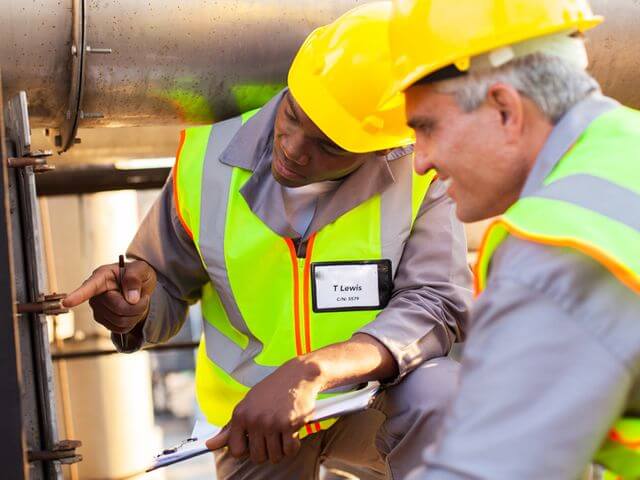
What is the Role of an Inspector?
QC Inspector (Contractor): The QC Inspector, typically from the contractor’s side, is actively involved in each phase of an activity. Their primary responsibilities include conducting thorough observations, assessments, and maintaining comprehensive documentation and records for every hold point inspection. This meticulous approach ensures that all project activities meet our stringent quality standards.
QA Inspector (Client / Owner): On the other hand, the QA Inspector represents the client or owner and primarily functions as an auditor. Their role involves observing the processes, providing advice based on their expertise, and verifying documents submitted by the contractor’s QC Inspector. If any uncertainties arise during inspections, they have the authority to conduct duplicate tests or inspections to ensure project conformity. Based on their findings and documented evidence, they can approve or reject submissions through formal inspection requests and reports.
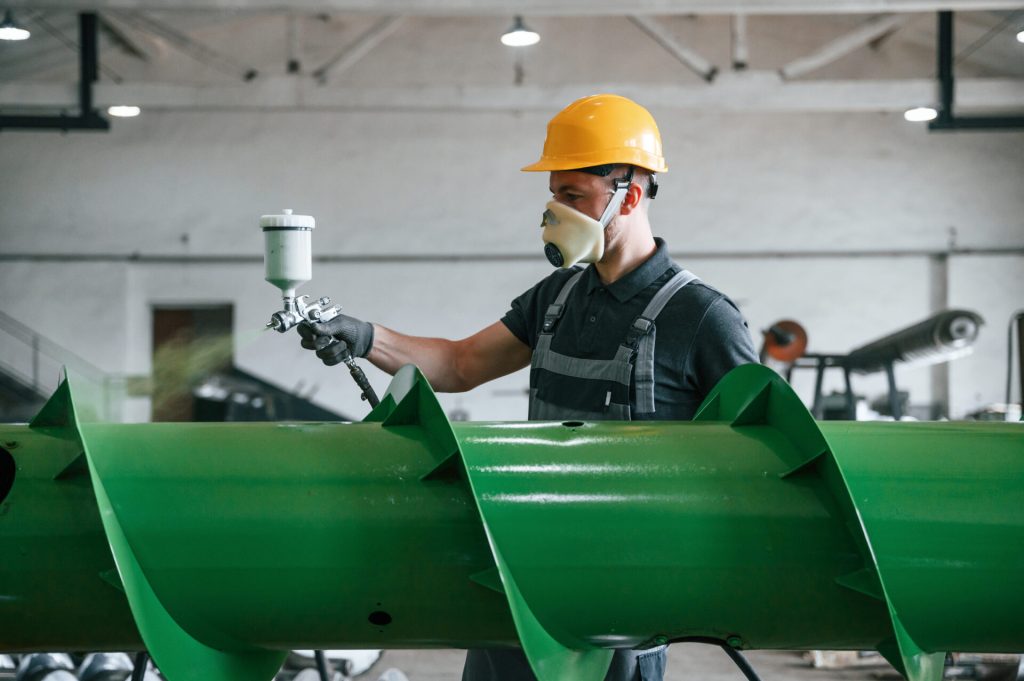
What are the Duties of an Inspector?
One of the primary duties is to be thoroughly familiar with all project-approved documents. This includes Specifications, Procedures, Inspection and Test Plans (ITP), Product Data Sheet (PDS), Safety Data Sheet (SDS), and any other relevant documentation.
It is crucial that an Inspector diligently obtains, reviews, understands, and interprets these documents comprehensively before embarking on any inspection activities. This preparation ensures that inspections are conducted accurately and in alignment with project standards.
By thoroughly understanding these documents, Inspectors can effectively ensure compliance and maintain the quality standards expected in our projects.
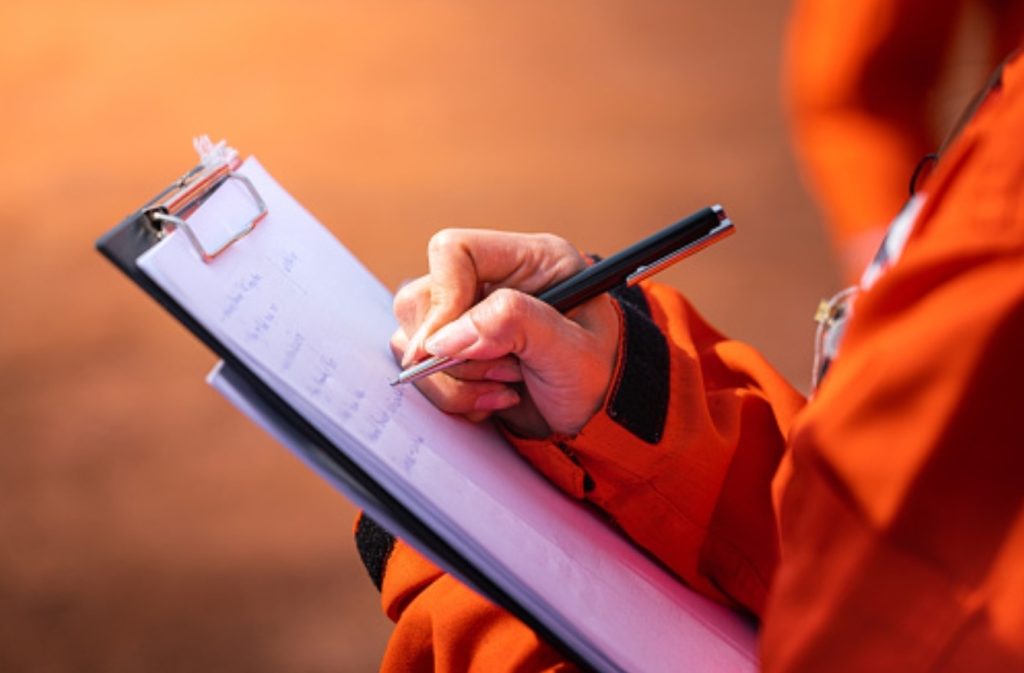
What needs to be reviewed & inspected?
Project Documents review:
The Inspector’s crucial role that a thorough review and understanding of all approved project documents play in ensuring our success. It is essential that the inspector meticulously review, understand, and interpret these documents.
Should Inspector encounter any deviations or ambiguities within the Project Specifications or Product Data Sheet (PDS), it is imperative to address these during the pre-job conference. Discussing and clarifying these issues before starting the coating activities will help avoid potential confusion or disagreements among our construction teams and Quality Control & Assurance personnel.
By taking these proactive steps, Inspector can ensure a smoother workflow and maintain the high standards that Inspector committed to achieving..
PQT (Painting or Production Qualification Test)
The importance of conducting the Painting or Production Qualification Test (PQT) before Inspector proceed with any official production activities. It is crucial that the PQT is meticulously performed, inspected, and accepted at every stage of the process, as outlined in Inspection and Test Plan (ITP).
For a successful outcome, it is imperative that the entire specified coating system related to the PQT undergoes thorough evaluation. This process should be completed with oversight from Client Inspector and Contractor QC Inspector. Additionally, while not always mandatory, having a representative from the Paint Manufacturer present can be advantageous for many projects.
Ensuring these steps are meticulously followed will not only uphold Inspector’s commitment to quality but also reinforce trust with any clients and stakeholders.
Material Receipt Inspection:
As Inspector prepare to embark on any upcoming coating projects, Inspector shall emphasize the critical importance of thorough Material Receipt Inspection.
Inspector success hinges on the careful verification and inspection of all materials, including coating and abrasive materials, as well as other related components. The Inspector has a pivotal role in ensuring project material compliance by checking the ordered quantities against the specific project requirements.
Key areas of Inspector’s focus include:
– Verification of Batch Certificates.
– Assessment of material packing conditions.
– Identification of any damages or expired stocks.
A meticulous inspection ensures that all materials conform to our high standards. The Inspector’s findings will guide decisions to accept or reject materials and allow for recommendations that ensure material conformity with project-specific requirements.
Inspector’s diligence in this process is crucial for maintaining commitment to quality and excellence.
Raw Material Inspection:
After Fabrication, before blasting and painting, the team will deliver at the blasting yard, that shall be inspected by the appointed Coating Inspector.
- Check the Material release note Vs actual materials received
- Check the condition of items (i.e. any damages or abnormalities)
- Check the Initial condition (Steel Grade A, B, C or D) and record
- If initial condition received against the project specified, either quarantine the materials or inform the client representatives for future warranty issues. This process shall be documented, witnessed and approved by the client before accepting contractor’s responsibilities.
- If the above initial condition inspection neither neglected nor carried out, the contractor shall be responsible for any intended warranty period as defined in the project contracts obligations.
- Instead of Initial condition “A”, if received “D”, the coating durability would be in question and debatable.
- Manufacturer Defects: Check for the manufacturer’s defects such as Slivers, Lamination or Hackle which shall be identified by the Inspector and rectified (removal by Grinding) before accepting for blasting. Failure to do so, possibility of premature coating failure is highly probable.
- Fabrication Defects: The raw materials (pipe, support) shall be processed by cutting, hot bending, grinding and welding. Once fabrication completed, the process related defects such as corners, edges, back-to-back angle and inaccessible areas shall be rectified (i.e. Grinding) inspected for smoothness without having protrusion that may cause premature coating failures.
- Chemical & Organic Contamination: The processed materials after fabrication perhaps dumped for long period that subjected to atmospheric influence (i.e. High humidity, Moisture, Condensation, Heavy Wind, debris, Metallic contamination by grinding, Salts exposure etc., All those visible and non-visible contamination shall be identified, rectified and inspected before accepting for blasting process.
- Check coating & Abrasive materials storage condition, record and advise in case of inferior storage against the manufacturer’s recommendations that may affect quality of materials.
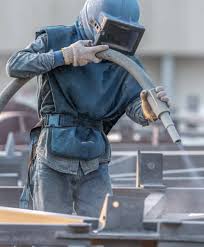
Before & During Blasting Inspection
- Traceability – Preserve / Mask / Identify by any means to avoid damages during blasting. After fully coated, the same identification information shall be transferred.
- Check compressed Air Quality Check (Blotter Test) ASTM D 4285 – Check for oil & water 2 Times daily
- Check Abrasives are new and clean if only new abrasive specified. Frequent surveillance inspection mandatory to check any malpractice by contractor construction team.
- Check Abrasive Quality Check Test (Conductivity / Size / Cleanliness) – ISO 11125 & ISO 11127
- Inspector / Test after Solvent cleaning process – SSPC SP 1. Any visible / non-visible contamination shall be rectified (repeated water wash with solvent cleaning) and inspected until satisfactory acceptance.
- If abrasive sieve analysis test kit not available at site, carry out Surface Profile yield test and record the average profile values.
- As a part of HSE requirement and consider yourself as Safety Lead, check all the equipment integrity and workability condition including all pressurized hoses conditions. If any damaged, inform the supervisor for replacement (But don’t raise NCR)
- Check the blasting pressure at the nozzle (using Hypodermic Needle Gauge) – 90-100 PSI for Mineral Abrasive and up to 125 PSI for Metallic Abrasive.
- Check the blasting nozzle to substrate distance – 12 to 18 inches ideally but maximum of 24 inches distance.
- Check blaster efficiency – Sweep blasting (40-60PSI / 45-60 Degree Angle) & Regular Blasting (90-100 PSI / 90 Degree Angle) – This is an optional observation; in case of any deviation, you may advise supervisor.
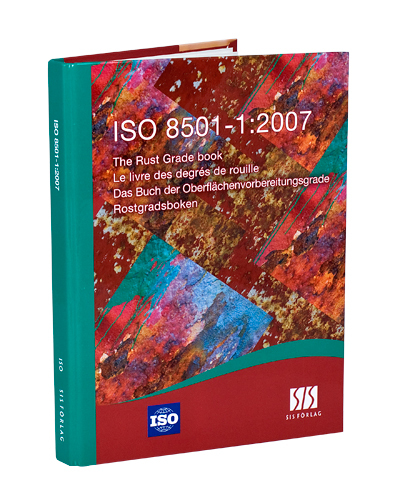
After Blasting Inspection
- Check for cleanliness using ISO 8501-1 pictorial representation, compare, inspect and accept against the specification requirement (Sa 1, Sa 2, Sa 2 ½ & Sa 3)
- Carry out surface profile measurement by using ISO 8503-2, record the value and accept if the values are within the specified parameters.
- Inspect dust level contamination as per ISO 8502-3, record the rating as per the specified requirement and accept.
- Check for spent abrasive residues if any, shall be removed before acceptance
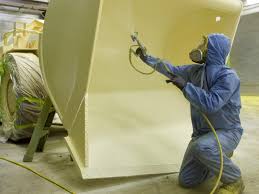
During Primer Application Inspection
- Check coating materials package conditions, if any opened shall be discarded / Quarantined
- Check, witness Coating materials mixing as per the Product Data Sheet
- Check both components shall be mixed homogeneously / Continuously by continual agitation as per the PDS requirements
- Check all the mixing procedure as per coating materials recommendation and PDS.
- Check Operator’s Training and certification details
- Check Manufacturer’s approval for coating applicator (Airless Sprayer)
- Stripe coat shall be applied on welds, edges, corners with the help of brush.
- Check the operator is following the coating application techniques and methodology (Selection of Tip size, Spray Pressure, Spray distance and spray angle etc.,)
- If any applicators found unsuitable or unqualified, shall be replaced with experienced operators. This process shall be recorded in daily inspection report.
- While spraying, check WFT measurement Vs NDFT (specified requirement)
- In case any in process application defects, shall be rectified immediately, otherwise lateral costly remedial action shall be actioned.
- Witness induction time, pot life as per the PDS or supplier’s application instructions.
- All the above process shall be witnessed, recorded and reported in Daily inspection report.
- In case of any deviation found, the work shall be stopped and rectified immediately. If contractor failed to oblige, the formal non-conformance report (NCR) shall be issued.
- Next day, the applied coating DFT shall be measured, recorded and accepted if satisfied as per the specified requirements.
- Otherwise, rectification shall be initiated, once again, inspected, recorded and accepted thru formal process.
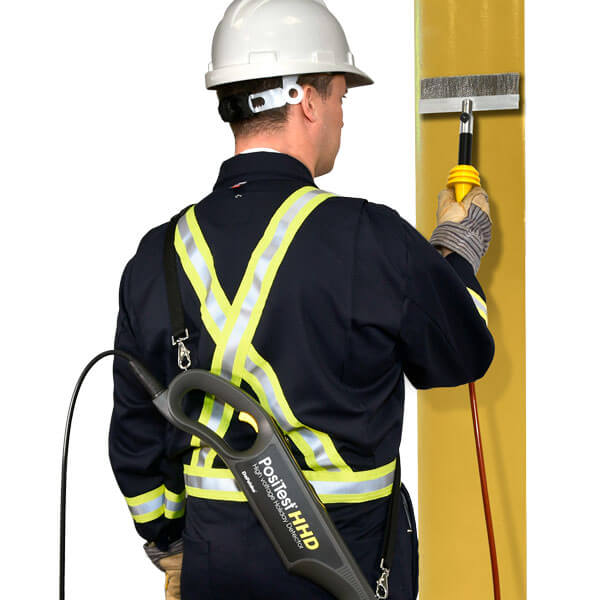
During Mid-Coat and Final coat application Inspection
- Repeat all the above procedures for every coat, record and accept if satisfied.
Final Acceptance Inspection
- Check Final DFT Vs Specified
- Accept if DFT within the specified range, otherwise, rectify, re-inspect and accept accordingly.
- Make sure that all the applied coatings shall be fully cured before carrying out Discontinuity check (Low or High Voltage Test), Adhesion Test and other needed test parameters.
- Record all the testing values (Qualitative or Quantitative), Accept as an Inspector
- Upon completion of your OADR, obtain Client QA inspector approval by getting signature for payment and fulfilment of contracts.